In this topic we will look at what are hazards and risk, and how to identify existing and potential hazards in the workplace, how to assess and eliminate or alter the risk factors. When you are dealing with many people during your workday it is necessary to be able to identify any risk that could potentially put their safety and yours at risk.
By the end of the topic, you will:
- Strategies for identifying common hazards in residential and home and community environments
- Signs and symbols to alert you to hazards
- Assessing risk
- Managing risk using the hierarchy of control
- Reducing manual handling risk
- Responding to emergencies including fire
Hazards and Risk in a Workplace: What Is Hazard?
Hazard means a source or a situation with a potential A hazard is something that has the potential to cause harm or injury. in terms of human injury or ill health, damage to property, damage to the environment, or a combination of these. Hazard identification means the identification of undesired events that lead to the materialization of the hazard and the mechanism by which those undesired events could occur.
The first step is to identify hazards around you by being alert and using tools designed to help. You can then work with your employer and colleagues to reduce or eliminate the risk. Collaboration and consultation are key to these processes.
Identifying hazards or risks in the workplace, generally start with conducting a Workplace Safety Inspection.
Watch
The following video from SafeWork Australia talks about conducting workplace safety inspections.
What is Risk?
A risk is the chance that an injury could occur as a result of the hazard, and what that harm could be. The level of risk is calculated by considering many different factors, such as the likelihood that harm could result, the severity of injury that could happen, and the steps you have taken to prevent harm. Risk is, at minimum, a two-dimensional concept involving
(1) the possibility of an adverse outcome, and
(2) uncertainty over the occurrence, timing, or magnitude of that adverse outcome. If either attribute is absent, then there is no risk. It is not possible to completely remove all hazards.
There will always be the chance of harm or injury. However, if we take care to think about what those hazards are, and how we can minimise them, we can work and provide support much more safely.
The following table outlines some examples of hazards that you might identify during the course of your work.
It is not possible to completely remove all hazards. There will always be the chance of harm or injury. However, if we take care to think about what those hazards are, and how we can minimise them, we can work and provide support much more safely.
This table to check out some examples of hazards and associated risks that you might identify during the course of your work:
Type of Hazard | Examples of Hazards | Examples of Risks |
---|---|---|
Manual Handling |
|
|
Infection |
|
|
Electrical and Chemical |
|
|
Equipment and Building |
|
|
Kitchen |
|
|
Flooring and Ground Surfaces |
|
|
Weather Related |
|
|
Behavioural |
|
|
Vehicles |
|
|
Human Error |
|
|
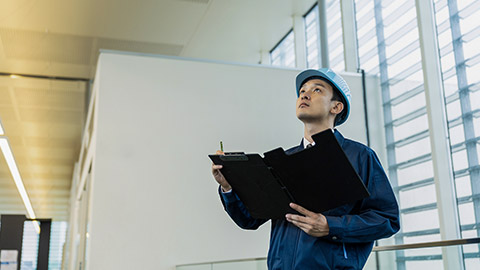
When accidents or injuries happen, there is nearly always a window of time in which the injury could have been prevented. Be alert to hazards around you, and it is more likely that you will catch this window and prevent an incident.
The three common procedures for identifying hazards in a workplace include:
Stay Vigilant!
- Look for hazards as you work
- If you have found a hazard: » Act quickly to remove it altogether (such as cleaning up a spill) OR » Isolate it (such as removing a faulty piece of equipment to a storeroom with a label to indicate that it cannot be used) OR » Report it as soon as possible
Use Hazard Inspection Checklists
- Use a checklist regularly
- Tick the areas in the checklist that could be hazards
- More detailed checklists are completed by senior management or health and safety representatives
Collect Information
- Managers collect information from incident and injury reports, near-miss reports, complaints and suggestions forms
- This information can help identify ongoing hazards
- You can help by reporting and documenting dangers in these reports
Reporting Incidents
A WHS incident report is an official document, generally developed as a form, to record the key details of an incident in the workplace. Most community service organisations will have their own WHS Hazard/Incident Reporting Templates and instructions on how they are to be completed.
Incidents can take many shapes from property damage, theft or security-related issues, accidents, injuries as well as ‘near misses’. The aim of an incident report is to record the basic information surrounding the incident. Information recorded should include: A brief description of the incident When did the incident occur? Who were the parties involved? Where did it happen? What was the incident type? (e.g. falls from height, traffic etc.) Was anyone injured? What were the injuries sustained?
Reporting in WHS typically includes:
- Incident Reporting - Informing relevant parties about accidents, injuries, illnesses, or dangerous occurrences that occur in the workplace. This may involve reporting to supervisors, managers, or health and safety representatives.
- Hazard Reporting - Identifying and reporting potential hazards or unsafe conditions in the workplace. This helps in addressing issues before they lead to accidents or injuries.
- Near-Miss Reporting - Communicating incidents or situations where an accident almost occurred but was narrowly avoided. Near-miss reporting is valuable for preventing future incidents by addressing underlying issues. Mandatory Reporting - In some cases, there are legal obligations to report specific incidents, such as serious injuries, illnesses, or dangerous occurrences, to regulatory authorities.
Read
To see an example of a Hazard/Incident Report Template, take a look at the following link.
Hazard Checklists
Hazard inspection checklists are tools used to systematically assess and identify potential hazards in a workplace. These checklists are designed to help individuals, usually safety officers or inspectors, conduct thorough inspections of the workplace to ensure a safe and healthy environment for workers. The checklists typically cover various aspects of the work environment, equipment, processes, and practices.
Watch
View the following video about hazards and risks for homecare workers in aged care and disability.
Read
To see examples of hazard checklists, click on the following link from SafeWork ACT.
Hazard Signs and Symbols
Safety signs are used to alert people to potential hazards, show the location of emergency and safety equipment or give instructions for dealing with emergency situations. Symbols and graphics save time in emergency situations. They can easily be identified and interpreted by people who are unable to read or understand a written language.
Here is a chart of safety signs and symbols that are commonly used in most settings:
Remember that workplace hazard identification, assessment and control is an on-going process that is best conducted in the context of full consultation between an employer and their employees.
Activity
Open the following WHS Office hazard identification PowerPoint slide from SafeWork (NSW). Drag each hazard item to the spot where you identify the workplace hazard.
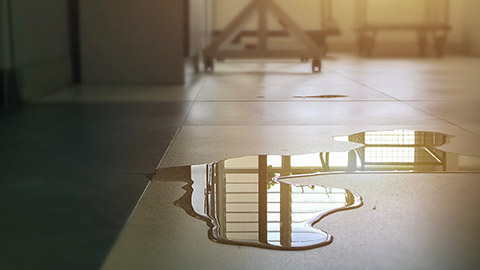
Common Hazards in Home and Community Workplaces
Hazards in home and community settings are affected by various unique factors. These include:
- You might be working alone, without supervision
- The spaces that you use, such as bathrooms, may have restricted spaces or hazards that contribute to slipping or falls
- You have less control over other hazards, such as a dog on the premises, fumes from chemicals or unsafe electrical hazards
- You might injure yourself or the client driving to and from a community visit or to a client’s home
- Your personal safety might be threatened by a client, family member or stranger.
Rights and Responsibilities in Home Environments
Workers delivering home-based services and their employers have the same WHS safety rights and responsibilities as workers in any other setting. You have the right to work within a safe environment and the responsibility to act sensibly to protect your own health and safety. You must always work within the service’s policies and procedures, even if the person asks you to do something differently. Clients are given a list of policies that they must follow to keep you safe while you are in their home. If they do not follow these rules, you have the right to refuse to enter the home, and your employer must back you up on this.
The policies differ between services and may include:
- The client or other members of the household should not smoke inside while you are present
- Equipment that you use must be safety checked
- The areas you use must be clear and free from excess clutter
- Dogs (apart from service dogs) must be contained outside or in a secure room while you are visiting
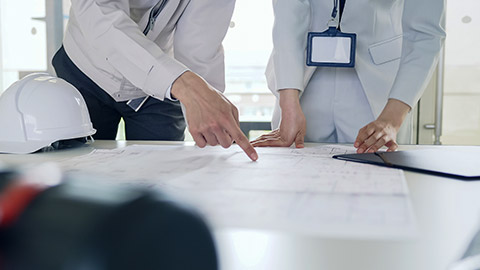
As you have seen, some hazards can be easily managed and even removed by making a small change. Others, however, require further investigation so that the problem can be managed most effectively.
A risk assessment is a formal process involving documents such as a risk assessment document. This helps staff to:
- Decide whether the risk is high enough to take action
- Consider how urgent the risk is
- Determine how the risk should be managed.
A risk assessment should be tailored to the workplace and to the type of activity being undertaken. For example, manual handling risks can be assessed using a manual handling risk assessment. Examples and templates for this type of risk can be found on health and safety websites such as Safe Work Australia or the website of your state or territory authority.
Below is an example of a risk assessment matrix that looks at the likelihood and consequence of a risk.
Once you have identified the hazard, it is time to consider appropriate risk controls.
- If it is not reasonable or possible to eliminate the risk, you and your service must do everything you reasonably can to reduce the risk as far as possible.
- Eliminating risks altogether, if possible, is the best way to do this.
The hierarchy of control is a tool used to help you to work through safety problems and reduce the risk. Here are each of the levels of the hierarchy of control.
Eliminating the Risk (Level One)
Eliminating the risk is the highest level in the hierarchy. Removing a risk completely is always the preferred option when available as it means there is zero chance of a future incident occurring. While it may not be possible to remove the risk completely in most cases, it should always be the first control measure explored. An example of risk elimination could be providing extending poles operated from the ground to access a high window latch rather than requiring climbing a ladder, which presents a risk of falling.
Substituting the Risk (Level Tw0)
The next level down in the hierarchy is risk substitution. Risk substitution is the process of removing risk by replacing it with another risk that is either less likely to occur or less severe in its potential damages. Substitution is less preferred to eliminate the risk completely as it still leaves a risk present, albeit in a reduced form. An example of risk substitution could be to replace noisy equipment with a quieter option or it could be replacing a highly toxic chemical with a less dangerous version. It’s important to conduct a new risk assessment after the substitution has been completed to identify any new risks created by the substitute process.
Isolate the Risk (Level Three)
The third level in the hierarchy is risk isolation. Risk isolation is performed by placing some form of barrier between the employee and the risk factor in order to provide protection. The key difference between this level and risk elimination (level one) is that the risk is still present, with the employee only shielded from it by the barrier. If the barrier were to fail or require bypass, the risk would return to being uncontrolled. Risk isolation could be enacted by placing dangerous machinery in a separate room from the operating and installing remote control systems.
Engineering Controls (Level Four)
Engineering risk control is the process of designing and installing additional safety features to workplace equipment. Safety features could be installing more stringent ventilation systems in noxious environments or installing guardrails on a raised walkway.
Administrative Controls (Level Five)
Level five of the hierarchy is administrative controls. These are measures the management and chain-of-command can implement to reduce the likelihood of a risk occurring. Measures could include providing dedicated training targeted at the risk or arranging work schedules to limit exposure times in hazardous environments.
Personal Protective Equipment (Level Six)
The final level in the hierarchy of risk control is the use of personal protective equipment (PPE). It’s likely that this level will be utilised regardless of what other levels are also being used to control risk. However, it remains at the bottom of the hierarchy as it doesn’t remove or reduce the risk itself. Instead, this level is designed around assuming an incident will occur and protecting the employee from harm when it does. Personal protective equipment includes hard hats, noise-reducing ear protection, or cut-resistant gloves.
The hierarchy of control is designed to be used:
- Collaboratively — Work through the tool with others, particularly other staff most affected by the hazard.
- Creatively — Work through the tool with as many ideas as possible for each category. You can later refine each idea in terms of whether it is possible or not.
- Systematically — Consider the highest levels of control, and work your way down until you are able to eliminate or reduce the risk as far as possible.
You can use a combination of controls across the hierarchy to provide the highest level of protection, as long as the top-level controls are considered first. Often you will need to use a combination of risk control measures to control the risk effectively.
Case Study
Case Study on Applying Hierarchy of Controls
Liliana’s managers asked her to help them to apply the hierarchy of control to a resident who has become more dependent and at risk of falling during a transfer. Working through each level, they considered the following levels:
- Elimination
- The resident has to be provided with support, so Lilianna and her manager both agree that eliminating the transfer altogether is not an option.
- Substitution
- They then consider options such as transferring with more than one worker at all times, using a hoist machine or using a standing machine.
- Isolation
- They considered the options of using guard rails or barriers when transferring the resident and limit access to high risk areas.
- Engineering
- Liliana suggests having a bedrail put onto the resident’s bed to help her to hold on during the transfer, but this is a risk to the resident’s safety while she is in bed because clothing might be caught around the rail. The manager also mentioned that it could be considered a restrictive practice if it prevented her from getting out of bed.
- Administration
- The manager suggested that training for staff by the visiting physiotherapist could help them to transfer the resident safely. Lilianna liked this idea.
- PPE
- This level of control was deemed not relevant to this problem, as it could not help with the safety of the transfer.
Using the hierarchy, Liliana and her manager agreed on the most effective controls:
- Using a standing machine to help the resident to transfer
- Having a training session with the physiotherapist to help staff perform the transfer via the machine more safely.
Watch
The following video discusses in detail the hierarchy of control and each stage.
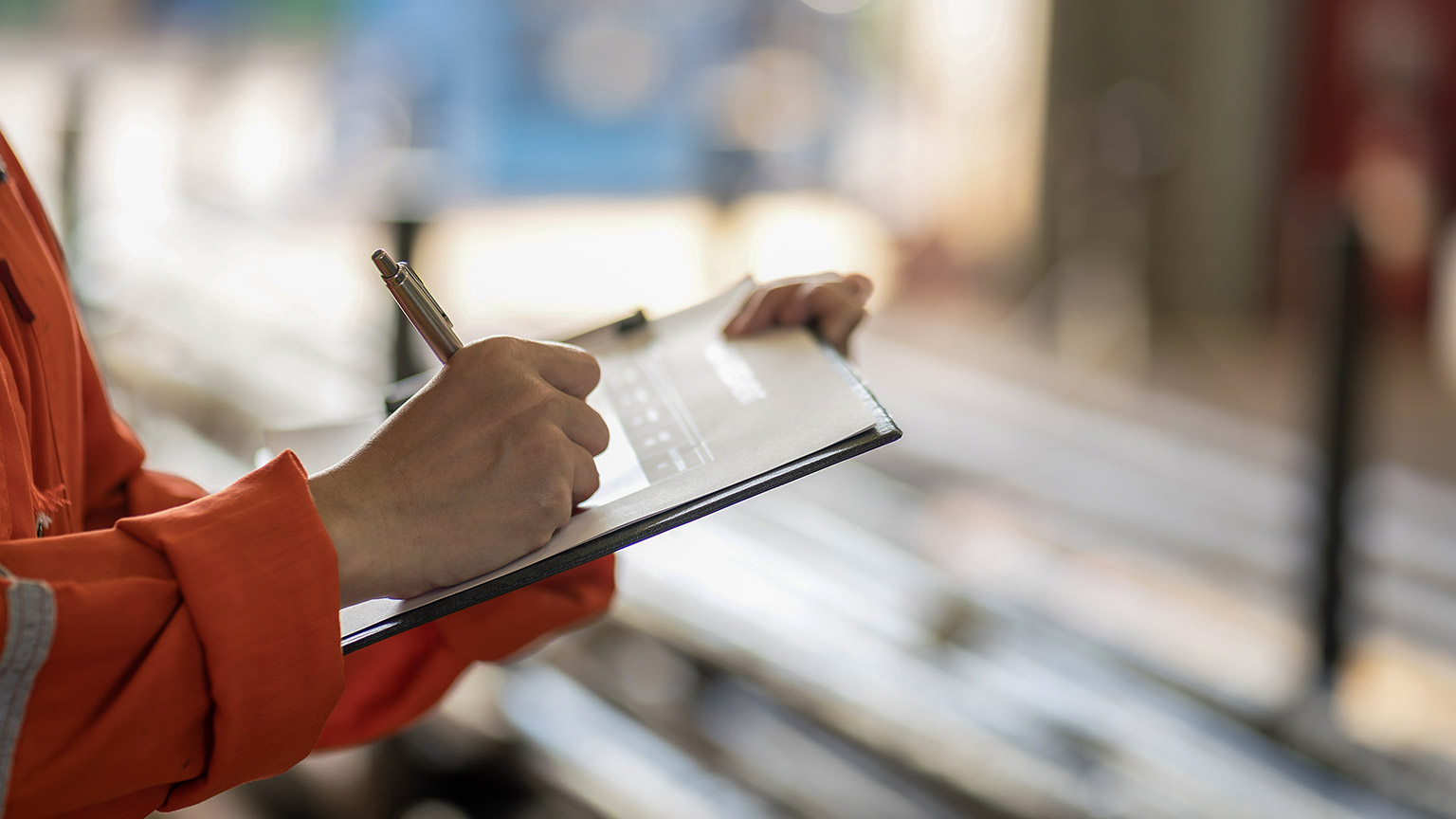