Welcome to Project Quality Planning.
This is the first topic of our Leading Quality Assurance module.
The learning outcome of this module is to evaluate and apply quality assurance processes to commercial construction work programmes.
Module 8 Introduction from Will
Click ‘Video Transcript’ or the plus icon (+) to expand and reveal the transcript for the previous video.
Welcome to this module on Leading Quality Assurance. The learning outcome of this module is to evaluate and apply quality assurance processes to construction work programmes. In this topic of Leading Quality Assurance, we will aim to cover the following: Workplace quality control processes, responsibilities and techniques to communicate quality assurance, and requirements for compliance with the quality assurance process. Remedial action where quality standards are not met. Procedure for final quality assurance checks of completed work. Let’s head into it.
What is quality assurance?
Have you ever bought a product and thought that its quality is top-notch? You may have felt that it was worth the money you spent on it. The same goes for construction projects. It is not enough to ‘do the job’. You need to strive to achieve top quality and maintain it.
Quality assurance (QA) refers to the process of preventing mistakes or defects in a product or service.
Both consumers and business operators want quality assurance. Consumers want quality assurance because they want to get their money’s worth. People do not want to spend money on defective things. This may cause them to go to other companies in the industry.
On the other hand, business operators want quality assurance to ensure they can compete in the market. Handing over a project with defects will give the business a bad name. This may result in losses or expenses (e.g. dealing with lawsuits due to faulty products or workmanship).
Several factors may affect quality assurance. These include:
- complexity of the product or service
- processes that the product or service undergoes
- complexity or level of precision required in the processes.
Nature of Quality Assurance
Quality assurance (QA) is the process of preventing defects or mistakes in a service or product. The key term here is the process. This process ensures that the product or service meets the specified requirements.
QA helps improve customer confidence and boost the business’s reputation in the industry. Companies that have excellent QA processes can ensure providing quality products or services. Their products and services meet the requirements and expectations of customers. This, in turn, makes customers happy and loyal to the business.
Principles of QA
The following are the principles of QA.
Fit for purpose
This means that the product or service produced matches its purpose. The product or service should meet the demands or requirements of the consumer. For example, a bulb should provide ample light to illuminate a room. If it is too dim or burns out after a few uses, it fails the QA.
Right the first time
This principle focuses on developing a defect-free product upon product release. This principle is also known as the zero-defect approach. This approach lessens the time and money spent correcting defects in the product or doing product recalls. This does not necessarily mean a perfect production process. Instead, this points out that all processes should strive to be done right the first time and every time.
Customer focus
Customer focus is identifying and meeting your customer’s wants and needs. When applied as part of Quality Assurance, the customer is the priority, and seeks their feedback to ensure you provide the highest quality to exceed their expectations.
Leadership
Leadership is pivotal in developing, guiding and driving the business to maintain the Quality Assurance system. A strong leader directs by example and ensures all aspects of the Quality Assurance system are being met for the business.
Plan-Do-Check-Act Cycle
The Plan-Do-Check-Act (PDCA) cycle is a continuous loop for the improvement of QA. It is simple and systematic, leading many businesses to adopt this approach for their QA. See the following explanations of each step of the PDCA cycle.
Plan
Objectives and processes for manufacturing a product or providing services should be clear. A clear objective and process can help distinguish a good product from a poor one.
Do
Work on the processes established. The processes may change as you work on the product. Testing of the product also occurs here.
Check
Observe how the process goes. Check if it aligns with the objective and follows the established processes.
Act
Personnel called testers should check if the processes need improvement. They will also recommend and implement necessary actions to improve the process.
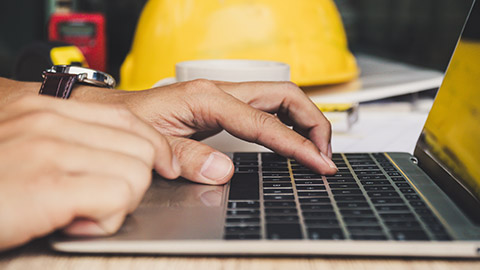
Methods for Quality Assurance
There are many ways to achieve quality assurance. But the following three are among the most notable ones on the long list of methods:
Benchmarking
Benchmarking is a process that involves measuring the performance of your business against a competitor in the same market. This will give you a better understanding of your business performance and potential.
Kaizen
This is also known as continuous improvement. This principle focuses on improving the process little by little—members of the business or organisation practising Kaizen work collaboratively.
ISO Accreditation/ISO 9000 and ISO 9001
The ISO, or International Organisation for Standardisation, develops the international standards for organisations. ISO accreditation ensures that a business's products and services are safe, reliable and of good quality.
ISO 9000:2015 describes the fundamental concepts and principles of quality management, which are universally applicable to the following:
- Companies striving for sustained success through the adoption of a quality management system.
- Customers seek confidence in an organisation's ability to consistently provide products and services that meet their requirements.
- Companies seek assurance in their supply chain that their product and service needs will be fulfilled.
- Companies and stakeholders aim to improve communication by establishing a common understanding of quality management terminology.
You may have heard of ISO 9001, the standard for quality management. ISO itself does not certify organisations for their standards. Instead, external bodies conduct quality assurance and management reviews based on ISO 9001.
Many organisations aim to get the certification for the following reasons.
- ISO 9001 standard gets reviewed and updated every five years. Thus ensuring that quality management processes are relevant and up-to-date.
- ISO 9001 is globally recognised, which can help boost an organisation's credibility.
- ISO 9001's quality management principles are tested and proven in the industry.
Manufacturers’ Literature
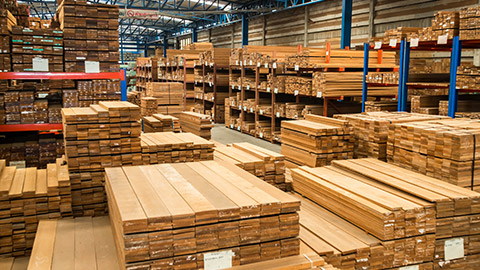
Manufacturers usually provide detailed information about their products, including their features, specifications, quality, installation instructions, and usage guidelines. This literature also typically includes information about product storage and any warranties offered. It's important to make sure you're using the most recent version of this literature to avoid potential safety hazards for yourself and others.
For example, if you're working with timber products in New Zealand, you might refer to the manufacturer's literature provided by companies like Carter Holt Harvey or Timspec. Their literature contains essential information about timber types, grades, treatment methods, installation guidelines, and safety precautions specific to New Zealand conditions and regulations. Always ensure you're using the most up-to-date literature to ensure compliance and safety on your construction projects.
The Branz "CodeMark"
The Branz "CodeMark" is a certification program that ensures building products meet quality standards. It's voluntary and offers a clear way for construction workers to verify the quality and design of a product before purchasing. This mark indicates that the product meets the requirements of the New Zealand Building Code or the Building Code of Australia, providing reassurance to buyers.
Branz is a well-known organisation in the construction industry, offering advice and education on various construction-related topics. Their CodeMark certification supports quality and best practices in construction. It's beneficial for manufacturers and suppliers as it helps endorse their product specifications and provides a marketing advantage. Certified products are recognised to comply with Building Code standards in New Zealand and Australia.
Have a look at the following link Good Practice Guides of the various Branz publication available.
Insulation material
Pink Batts: Lightbulb Advertisement 2008 - Adspot
One specific example of a product certified with the Branz "CodeMark" is a type of insulation material commonly used in residential construction. This insulation material comes with the CodeMark certification, ensuring that it meets the required standards for fire safety, thermal performance, and durability as specified by the New Zealand Building Code. Builders and contractors can rely on this certification to confidently select and install the insulation material, knowing that it complies with the necessary regulations and will contribute to a safe and energy-efficient home.
Some examples of well-known brands that may have insulation products with CodeMark certification include Pink® Batts, Earthwool®, and Mammoth™. These brands offer a range of insulation solutions designed to meet the requirements of the New Zealand Building Code while providing effective thermal and acoustic performance in residential buildings.
As stated earlier, QA boosts the customer’s confidence and the business’s reputation. Thus, each company should develop its QA processes. There are three steps in developing a process.
Develop business goals and objectives related to quality
Define what quality is. Base your definition on the requirements or expectations of the customer. As for the objectives, ensure that it aligns with your business goals and objectives. The alignment ensures that your QA processes are still on track to achieve your goals.
Identify roles and responsibilities of personnel
Ensure that the roles and responsibilities of involved personnel are clear. Clarity on these aspects ensures a smooth process and avoids redundancy in QA. The personnel you assign should also have the necessary skill set for the tasks. Remember, you want to ensure quality. Therefore, you should delegate the correct personnel for the task.
Develop the QA process and policies and procedures
Developing quality assurance policies and procedures ensures the business complies with regulatory policies for quality. It assures that the steps and actions to follow the procedures are the same for everyone in the business. This is why choosing the appropriate personnel is vital in Step 2. They ensure the processes are correct and you use the right tools or metrics. The following graphic shows some essential things to consider when developing your QA process.
Evaluating and reviewing QA processes
QA processes should strive for continuous improvement. Improvements can help streamline the process and make it more efficient. Thus, it is crucial to evaluate and review your QA processes. Evaluation allows you to check how the performance of your QA processes. On the other hand, review involves studying the results and making decisions based on them. These two should come hand-in-hand when improving the QA process. To improve your QA process, you can implement the following steps.
Review industry and legal standards
These are important to ensure you are avoiding compliance risks while ensuring quality. Remember, different laws apply to various business operations. These legislations have different compliance requirements for business operations. The following list is an example of legislation you can associate with your QA processes.
Analyse the results of your QA
Evaluate the results of your processes. Ensure to check the metrics when evaluating your QA processes. It would be best to check your company’s business culture as well. This culture refers to a set of practices, values, and expectations in your business. Put simply, it is the culmination of traits observed in your company. Ensure to include this in your review. Doing so will help you cultivate a strong culture of QA in your operations.
After that, proceed to the review. Identify which processes require changes or improvements and what you can retain.
Adapt as necessary
You must take this step if you find inconsistencies or errors in the previous step. This allows you to improve and make the process more efficient. Implement the changes needed and test them again. Repeat this step until you can no longer find process inconsistencies or gaps.
Communicate the results with the team
After finalising the process, ensure to communicate it with the team. This will help them apply the QA process when developing the product. Failure to do so will result in poor quality of products due to outdated QA processes.
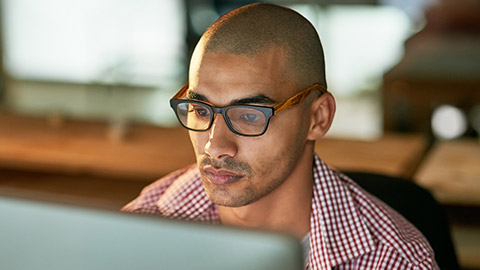
Ultimately, the responsibility of ensuring quality compliance at the project level and executive management at the organisational level sits on the project manager. However, you may be tasked with locating and interpreting quality policies and procedures as part of your project role. Therefore, it is crucial that you are aware of this aspect.
Once you have accessed and sourced the relevant policies and procedures that apply to your project, all activities and decisions regarding quality management planning must be consistent with those policies and procedures. All project team members must take personal responsibility for complying with them.
The quality management, quality assurance, and quality control activities to be embedded in the project plan and processes must be aligned with the policies and procedures.
Policies and procedures that must be adhered to include:
- legislative requirements, for example, environmental or work health and safety legislation
- relevant industry standards, professional standards, and codes of practice
- organisational policies, processes and procedures, company production standards and specific management directives
- your organisation’s key performance indicators (KPIs)
Each project task will need to satisfy the established quality criteria and comply with the relevant policies and procedures.
Sources of Policy and Procedures
Consider the following sources to find the appropriate quality policies and procedures that apply to a specific project.
ISO standards in Standards New Zealand
Standards New Zealand is an independent business unit within the Ministry of Business, Innovation and Employment (MBIE). Standards are developed in partnership with Standards Australia by working with the government, various industries, and the community. These define internationally recognised and adapted standards for product and service quality.
Local government legislation
These are the directives proposed by legislative bodies.
Conditions of permits, contracts, etc
These are the accompanying agreements from your project’s permits and contracts. The policy and procedure to be observed may not be explicitly laid out in these documents, but these serve as a further guide in defining what must be done and how to go about your current project.
Industry codes of practice
These are the sets of rules and measures that are put in place to regulate industry conduct and are applied to its workers and their relationship with their clients. The codes of practice support legislative requirements relevant to the industry and improve the industry standards.
Technical specifications and plans supplied by your client
Your client’s technical specifications and plans must serve as standards by which the project processes must be carried out to deliver the desired outcome.
Your own organisation’s policies and procedures
Your organisation’s existing policies and procedures define how quality management and other project-related tasks and activities are to be done. These policies and procedures will heavily influence how different processes in maintaining project quality will be implemented.
Your client’s corporate policies and procedures
As policies and procedures may vary from organisation to organisation, you must consider your client’s corporate policies and procedures to ensure that the processes and projects you undertake comply with their policies and procedures.
The ISO 10006 standard provides guidelines for quality management in projects. It covers the following main areas:
- quality management systems in projects
- management responsibility
- resource management
- product realisation
- measurement, analysis, and improvement
Other specific guidelines may be embedded in your organisational policies and procedures and the specific project documentation (e.g. quality management plan).
Explore
This link is an example of a quality policy document from Splice Constructions Ltd.
Locate and interpret a quality policy or procedures document from your company's repository.
Do you think that you and your team adhere to the quality policies and procedures?
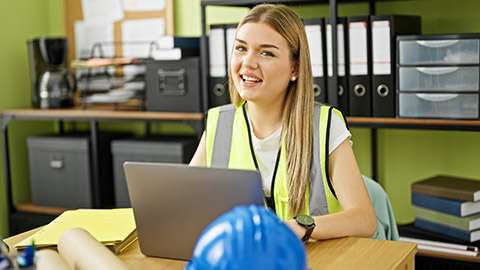
It is the primary responsibility of your project manager to develop the overall project plan, which includes the quality management plan. The project quality requirements and project deliverables quality criteria you contributed to developing are integrated into the quality management plan that will define the quality standards and guidelines the project processes must comply with.
As a project team member, regardless of your role, you will no doubt be required to contribute to developing the quality management plan. As discussed earlier, you may have contributed to determining the quality requirements and developing the quality criteria as part of a team process or as an allocated task according to your role or area of expertise.
You may also have contributed by researching and identifying the organisational policies and procedures, legal requirements, and required industry standards that apply to the project. Once the quality standards, requirements, and applicable policies and procedures are defined, they must be documented in the quality management plan and embedded into the project processes.
Quality management plan
To ensure these quality requirements are met, all the quality standards and guidelines you have learned to develop and identify thus far must be laid out in your project’s quality management plan. The quality management plan must document the developed quality requirements, criteria, and standards. More specifically, your project’s quality management plan should include the following:
- quality objectives and definitions
- quality criteria that must be met
- quality standards that must be achieved
- policies and procedures that must be complied with
- any legislation that must be complied with
- levels of performance required
- quality management tools and methodologies
- quality assurance processes
- quality control processes
- authorisations and responsibilities (including the identification of experts to conduct audits/check quality throughout the project)
- change request processes that could impact the quality
- continuous improvement mechanisms
- tools, procedures, and techniques to be used
Most organisations will have a standard approved format for developing the project plans. You might contribute to preparing the documents in several ways, depending on the project tasks assigned. A common practice is dividing the plan and assigning various tasks to the team members. You might have individual responsibility for certain aspects or work in pairs or groups to complete each section. The process will involve collating and copying the established quality requirements into the project plan template.
The project quality management processes and procedures are carried out according to this plan.
Below is a sample Quality Management Plan template from Prince2™.
Once the project plan is complete, it is sent for approval and sign-off by higher management and, in some cases, by the sponsor or client.
Developing quality requirements in project processes
As shown in the Quality Management Plan template in the previous section, standards for planning, quality assurance and quality control must be specified. Those criteria and standards will be the benchmark for performing the activities involved.
Below is a table of the commonly performed activities of each of the three processes in quality management and sample quality requirements for each.
Quality Processes | Common Quality Activities | Sample Quality Requirements |
---|---|---|
Quality planning |
|
|
Quality assurance |
|
|
Quality control |
|
|
Remember that the quality requirements in the project plan and processes that you contribute to identifying must be specific and relevant to the project.
Developing quality activities exercise
Using the Documentation Tool below, insert your answers to the prompt provided. Share and discuss your answers during one of the Live Sessions with your tutor and peers.
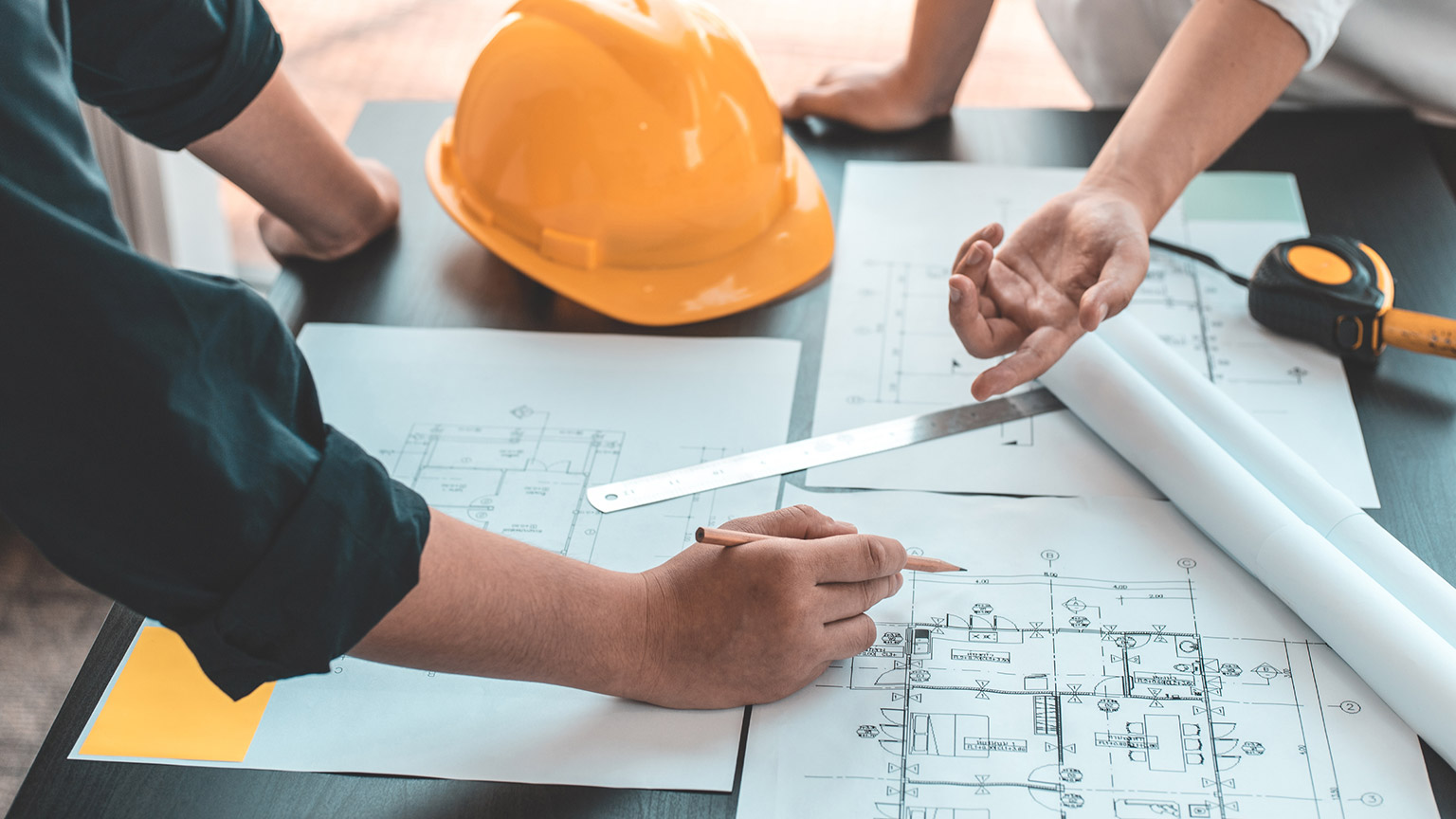