A lot of tools make up the toolkit for an electrician. In this topic we look at what they are and what they are used for. You will:
- Identify hand and power tools used for common electrical jobs, their care, and the possible dangers associated with their use.
- Look at multimeters and other key tools for measuring and checking electricity
In your learning on campus, you will have plenty of opportunity to put your knowledge of these key electrical industry tools to practice.
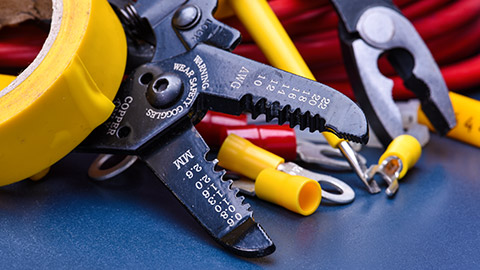
What we're covering:
- Hand tools – wire strippers, insulated screwdrivers
When you're on the job, your tool kit becomes your best friend. It's what helps you apply your skills and make sure everything is safe and reliable. Without the right tools, electrical work just can't be done properly. Tools may be categorised as:
The following is a list of must-have tools for your toolbox. These tools will help you do your job effectively, whether you're installing new systems, fixing problems, or doing regular maintenance.
Hand tools
A hand tool is any tool that is powered by hand without motor. On a piece of paper, list all the hand tools an electrician might use on a daily basis.
WIRE STRIPPERS
Electricians use wire strippers to cut through the protective sheath of cables to access the conductive core. The stripping process ensures that only the necessary amount of pressure is applied to prevent damage to the copper wires.
Proper wire strippers speed up the job, make it easier to work with wires, and result in neater connections between wires, and terminals or connectors.
Types of Wire Strippers:
- Adjustable Strippers - Versatile tools that can handle stripping, crimping, and wire-snipping tasks.
- Triple Action Wire Strippers - Designed for thicker cables with tough insulation, utilizing a unique spiral cutting motion.
- Wire Stripper Pliers - Suitable for thicker, multicore cables, featuring V-shaped stripping jaws.
- Sheath Strippers - Utilize a rotary action to produce a neat ring cut while stripping.
- Pistol Wire Strippers - Have a self-adjusting blade and use a compound stripping action with a firm grip.
- Automatic Wire Strippers - Use a mechanism to rapidly remove insulation and cut wire with a single application of pressure.
- Manual Wire Strippers - Standard hand-operated models usually with a spring-loaded handle and safety lock.
Wire strippers are also referred to as cable strippers or cable wire strippers. Some wire strippers are capable of handling twin and earth cables, which enhances their versatility.
Activity
Below are some questions relating to wire strippers. Bring your to class to discuss with your tutor and your classmates.
- What is the purpose of using wire strippers in electrical work?
- Describe the function of 'Triple Action Wire Strippers'.
- You need a thicker multicore cable for an electrical project. Which type of wire stripper would you chose and why?
- In what situations would 'Automatic Wire Strippers' be particularly advantageous?
INSULATED SCREWDRIVERS
Screwdrivers are a fundamental and indispensable tool for electricians due to their versatility and precision. Electricians use screwdrivers to access electrical containers, install and remove electrical components, make wiring connections, adjust devices, and perform repair and maintenance work. They are crucial for mounting fixtures and devices, accessing electrical panels, and ensuring proper grounding and bonding.
The operation of screwdrivers relies on the application of torque, which is rotational force, exerted when the screwdriver's head is inserted into the slot on the screw.
Electrician's screwdrivers feature carefully designed insulated handles, ensuring protective electrical resistance. These insulated handles are crucial to safeguard electricians against potential electrical hazards while working with live electrical components. The VDE approval indicates compliance with safety standards for electrical applications.
Safety is crucial, necessitating that all screwdrivers are insulated up to 1000V to protect against electrical shock and arcing.
Screwdrivers come in various sizes and shapes, offering compatibility with the wide range of screw designs encountered in electrical work. Driver tips are the key point of differentiation.
Amongst the most prominent are:
- Slotted Screwdrivers - have a single, flat blade that fits into straight-line slots on screws. They are commonly used in older electrical equipment and various general applications.
- Phillips screwdrivers - have a cross-shaped tip with four arms, designed to prevent over-tightening. They are widely used in electrical work, electronic devices, and other applications.
- Pozidriv screwdrivers - have a similar cross-shaped tip like Phillips, but with additional notches for improved torque transmission. They are commonly found in modern electrical appliances, industrial equipment, and certain construction materials.
Activity
Activity
Your task is to investigate insulated tools and their significance, especially in electrical work. Follow the steps below to understand what insulated tools are, why they're essential, and how they enhance safety.
When you are finished present your findings as an A4 poster and post on the class forum.
INTRODUCTION TO INSULATED TOOLS
Begin by searching for a simple definition of insulated tools. Understand the basic concept of how these tools are designed to keep workers safe during electrical tasks.
Safety and Prevention
Explore the importance of using insulated tools for safety. Learn how they prevent electric shocks and accidents by acting as a barrier between you and the electricity.
Types of Insulated Tools
Identify a few common types of insulated tools used by professionals. Focus on tools that electricians and other professionals use when working around electricity.
Benefits of Insulated Tools
Discover the advantages of using insulated tools. Look for benefits such as protection against electric shocks and the safeguarding of equipment.
Task Using Insulated Tools
Research how to correctly use insulated tools. Find any guidelines or tips that help you ensure your safety and the tool's effectiveness.
Real Life Examples
Look for any real-life stories or examples where insulated tools have made a difference. These stories will give you practical insights into the impact of using these tools.
Conclusion
Reflect on what you've learned and think about how this knowledge can be applied to future tasks and situations involving electrical work.
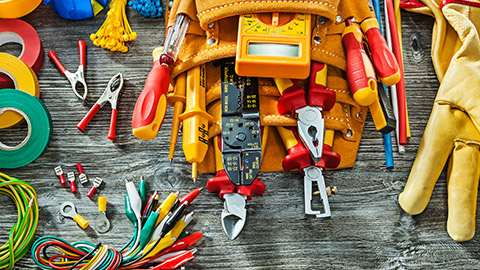
What we're covering:
- Hand tools – insulated pliers, cable cutters, spanners, safety knife.
This lesson on hand tools continues from the previous lesson.
INSULATED PLIERS
Pliers have been used for a long time due to their ability to accomplish tasks that require torque more effectively than bare hands alone. Modern pliers are typically made from steel, providing a robust grip and ensuring durability in challenging work environments.
Different types of pliers are available - each designed for specialised tasks. Some types of pliers used in the electrical workplace include:
- Combination Pliers - Multifunctional tools for cutting wires, stripping insulation, and gripping, replacing the need for multiple tools.
- Long Nose or Needle Nose Pliers - Essential for delicate electrical tasks, gripping small objects, and accessing tight spaces.
- Slip Joint Pliers - Adjustable jaw span, ideal for nuts, bolts, and fasteners for a secure grip. (Slip joint pliers are also referred to as Pump, Tongue-and-Groove, Channel Lock, or Adjustable Pliers.)
- Side Cutting Pliers - Designed for easy and precise wire cutting in tight areas and electrical boxes.
- Locking Pliers - Securely lock onto objects for a strong grip, useful for metalwork.
- Terminal Crimping Pliers - Create secure and reliable crimp connections for electrical terminals and connectors.
Insulated pliers are essential for performing a wide range of fiddly electrical tasks, especially when dealing with wires. The insulation provides protection against electrical shocks, ensuring the safety of the electricians. Buy high-quality insulated pliers from reputable brands to ensure durability and reliability during electrical work.
Activity
CABLE CUTTERS
Cable cutters, also known as wire cutters, are heavy-duty pliers designed specifically for cutting thick cables and wires cleanly and efficiently. Their sharp blades provide clean and precise cuts through various types of cables and wires. Consider the cutting capacity of the cable cutter, which ranges from 0.4mm to 600mm, ensuring it meets the requirements of the job.
Cable cutters used in electrical applications are typically insulated to prevent electrical shocks. (Fully insulated cable cutters are essential when working with high-voltage wiring.) It is important not to confuse the plastic or rubber coating on the levers of a non-insulated cable cutter for being electrical insulation.
Cable cutters don’t just cut cable, they also bend, hold, twist, or strip small gauge wires and are made to be very precise. They provide a handy way to strip off insulation for crimping and similar operations quickly.
SPANNERS
Spanners are among the most useful and versatile tools in an electrical toolkit. Besides handling nuts and bolts, they can be used as clamps, grips, or even levers when needed. Their multi-functional nature makes them indispensable for various tasks encountered in electrical work.
Proper selection and use of spanners are crucial for safe and effective electrical work. Different sizes of bolts and nuts require various spanner designs to ensure a close fit between the head which applies torque and the fixture in question. Size is equally important in order to achieve a tight grip.
Common spanner models:
- Adjustable spanner - Features a moveable jaw that can be adjusted to fit different sized bolts or nuts. Often referred to as a monkey wrench, it offers versatility in handling various fasteners. A must-have tool for dealing with different sizes of nuts and bolts during electrical installations and repairs.
- Open Ended Spanner - Consists of a double C-shaped clamp in different sizes at either end. Ideal for situations where space is limited, allowing easy access to fasteners in confined spaces. Useful for tightening or loosening nuts and bolts found in electrical panels and equipment.
Tips:
- Ensure you have spanners in different sizes to handle various fasteners encountered in electrical installations.
- Use the spanner at the correct angle and avoid excessive force to prevent damage to the fasteners or the tool itself.
- Regularly clean and maintain spanners to prolong their lifespan and maintain their effectiveness.
Activity
Answer the following questions and bring your responses to class to check with your classmates and tutor.
- What is the purpose of using an adjustable spanner?
- How does an open-ended spanner differ from an adjustable spanner?
- Imagine you needed to work on a nut located in a tight place within an electrical panel. Which type of spanner would you choose and why?
- Why is it important to regularly clean and maintain your spanners?
SAFETY KNIFE
As an electrician, wire cutting is a common task, making a sharp utility knife an essential addition to your toolbox. Safety knives with smaller blades make it easier to cut wires securely. Safety knives are known by various names: Stanley knives, utility knives, pen knives, or box cutters.
The key feature is that the knife blade is shielded for safety when not in use, minimising accidents and injuries. Some models have spring-loaded sliders that automatically retract the blade after use.
Safety knives come in different shapes and sizes for various situations. Professional safety knives for electricians have handles made from aluminium, plastic, or steel. The blade material can be stainless steel, carbon steel, or tool steel for maximum cutting power. The blades in safety knives are often replaceable when broken or dulled, and some utility knives feature snap-off blades that offer a fresh cutting edge when needed.
Safety is crucial when using a safety knife. The small and movable surface of wires increases the risk of blade slipping.
Activity

What we're covering:
- Hand tools – hacksaws, hex keys, claw hammer, chisels, torch, crimps, etc.
This lesson continues the learning started in the previous two lesson.
HACKSAWS
A hacksaw is a type of hand tool designed for cutting through various materials, including plastic, steel, and other metals. It features fine-toothed saws, enabling clean and precise cuts in metal. Electricians often rely on hacksaws to cut metal conduits and pipes during installation and repairs, and they also prove useful for trimming electrical boxes and brackets when needed.
The hacksaw features a thin, flexible blade held at tension in an adjustable frame connected to a pistol grip handle, ensuring a comfortable and firm grip during cutting tasks. The blade's tension can be easily adjusted to suit various cutting requirements. The blades are replaceable when they become dull or broken, providing convenience and efficiency in the tool's maintenance.
Hacksaws are produced in a variety of shapes and sizes to support a range of applications and industries. In New Zealand, hacksaws are available in both metric and imperial sizes. The main types of hacksaws include:
- Senior hacksaws or full-sized hacksaw - large, versatile tools that are straightforward to operate and excel at cutting tougher materials.
- Junior hacksaws - a smaller saw used when space is limited, or more precise cutting is required. They feature softer, half-sized blades and are not suitable for cutting harder substances. Junior hacksaws are compact, easily portable hand tools.
Activity
When using a hack saw for cutting tasks as an electrician, what safety precautions should you take to ensure your well-being and prevent potential hazards? (Describe a minimum of five.)
Bring your answers to class compare with your classmates.
HEX KEYS
Hex keys, also known as Allen keys or Allen wrenches, get their name from the hexagonal fasteners they adjust. They come in various materials like steel, nickel, bronze, or copper alloys.
Types of Hex Keys include:
- Straight Hex Keys - Used as extensions to screwdrivers, they apply torque to hexagonal fastenings.
- L-Shaped Keys - Have identical heads at both ends, offering different leverage. The shorter end provides more leverage, while the longer end allows access to confined spaces.
- Folding Hex Keys - Convenient and easily stored due to their folding design.
- T-Handle Hex Keys - Feature ergonomic handles for a firmer grip and improved control.
Hex keys are essential when working with hexagonal fasteners and fixings in various electrical devices and equipment. Some handy tips are:
- Always use the correct size of hex key to avoid damaging fasteners and to ensure a secure fit during adjustments.
- Keep hex keys in a well-organised toolbox to prevent misplacing or losing them.
- When using hex keys, make sure to apply steady and even pressure to avoid stripping or rounding the fastener edges.
- Regularly inspect hex keys for signs of wear and replace them if they become damaged or worn out.
- Familiarise yourself with the different types of hex keys and their specific applications to work efficiently and safely in electrical installations and repairs.
CLAW HAMMERS
Claw hammers are versatile tools used by electricians and other tradespeople. One side of the hammer features a standard head for driving nails and inserting fixtures. The other side of the hammer has a dual steel claw designed to provide a robust grip, making it easy to remove nails and similar fixtures.
Claw hammers are useful to gain access to sealed spaces, such as fuse boxes hidden behind paneling or other fixtures.
Some handy tips to consider are:
- When using a claw hammer, ensure proper technique and precision to avoid accidents and damage to the materials.
- Maintain the hammer's claws in good condition by regularly checking for wear and sharpening or replacing them when needed.
- A comfortable and ergonomic handle is crucial to reduce strain and fatigue during prolonged use.
- Keep the hammer clean and dry to prevent rust and corrosion, which can affect its performance.
- Always wear appropriate personal protective equipment, such as safety glasses and gloves, when using a claw hammer to prevent injuries.
- While it's not necessary to invest in the most expensive make or model of claw hammer, it is important to choose a high-quality hammer that can perform the job effectively and safely. Choose the one that best suits your needs and preferences as an electrical worker.
CHISELS
Chisels are powerful and versatile tools used for breaking through various materials like wood, stone, brick, concrete, and others. Despite their ancient origins, chisels remain essential and effective in modern times for various applications. Modern chisels are typically made from various steel alloys, providing durability and strength.
Electricians often use chisels to create channels in walls for running electrical cables, conduits, and other wiring, making them a valuable tool during installation procedures. Popular sizes of chisels to keep in your tool kit as an electrical apprentice include 5mm, 10mm, 16mm, 18mm, 20mm, and 50mm.
- When using chisels, ensure you have a firm grip and use appropriate striking tools, such as a mallet or hammer, for effective and safe cutting.
- Always wear proper personal protective equipment, like safety glasses and gloves, when using chisels to protect against potential injuries.
- Regularly inspect chisels for signs of wear and maintain their sharpness to ensure efficient cutting performance.
- Store chisels properly in a designated tool holder or toolbox to prevent damage and to keep them easily accessible.
- Familiarise yourself with the different types of chisels available and their specific uses to effectively apply them in electrical installations and repairs.
TORCHES
Torches are essential items that every electrical worker should have in their tool kit for various situations. Many different torch designs are available, but smaller torches powered by LEDs are typically favored by professionals due to their lightweight and easy portability while providing sufficient illumination.
Torches play a vital role for electricians, allowing them to work in darkened areas, such as buildings where the lighting has failed or when the power is switched off for safety reasons.
Head torches, which can be attached to helmets or hats, are particularly useful when both hands are required for precise work in dark or confined spaces.
Magnetic torches, which can be attached to metal surfaces, provide added convenience and versatility during electrical work.
Handy tips to consider are:
- Ensure torch has sufficient battery power before starting any task to avoid disruptions and potential hazards.
- Always carry spare batteries or a charging source for your torch to avoid unexpected power outages during critical work.
- Regularly check and maintain torches to ensure they function optimally when needed.
- Invest in high-quality torches to ensure durability and reliability in demanding electrical environments.
- Use the torch responsibly and be considerate of others in shared workspaces to avoid disturbing co-workers or causing accidents.
- Properly store torches in your tool kit or designated compartments to prevent damage and ensure they are readily accessible when required.
CRIMPS
Crimps are small metal connectors used in electrical and electronic applications to join or terminate wires and cables. Crimps are designed to create a secure and reliable electrical connection by being crimped or compressed onto the wires.
Crimps come in various shapes and sizes, depending on the specific application, including butt splices, ring terminals, spade terminals, and more. The appropriate crimp should be selected based on the task requirements.
Properly crimped connections not only provide reliable electrical conductivity but also contribute to the safety and longevity of electrical systems.
Crimping tools, also known as crimpers or crimping pliers, are specialised tools used to apply even and controlled pressure to crimps. Electricians should use crimping tools that match the type and size of the crimps they are working with. Using the correct tool ensures precise and effective crimping, preventing potential issues like loose connections or damage to the wires.
ELECTRICAL TAPE
Electrical tape, also known as insulation tape, is a self-adhesive and pressure-sensitive tape used to insulate wires and other conductive materials. Its primary purpose is to protect the sensitive conducting core within electrical wiring from external elements such as abrasion, heat, liquids, and environmental factors. It helps keep wires organised and secure, reducing the risk of electrical hazards and improving the overall safety of the system.
Electrical tape is made from various materials, including PVC, vinyl, copper foil, and glass cloth. Different varieties offer varying characteristics such as colours, widths, thicknesses, temperature tolerance, adhesion strength, and insulating capabilities.
A high-quality electrical tape should be water and heat-resistant, self-adhesive, and flame-retardant. These features enhance the tape's performance and longevity in various environments. Store your electrical tape in a dry and cool environment to maintain its adhesive properties and prevent deterioration.
While black is the most commonly used colour for general insulation, having a variety of colours in your toolkit is beneficial for differentiating wires and organizing complex wiring systems. Recall the colour-coding system in New Zealand:
- Green/Yellow combination indicates the protective earth or ground wire.
- Green tape alone may be used to signify the protective earth or ground wire, though the green/yellow combination is more common.
- Blue tape is often used to identify neutral conductors in LV applications.
- Red tape is used to mark low-voltage AC (alternating current) conductors.
- Black tape is generally used for general insulation purposes and to indicate the low-voltage neutral point in a circuit.
- Brown tape is used for marking live or phase conductors in single-phase systems.
TORPEDO (SPIRIT) LEVEL
A torpedo (spirit) level is an essential tool when placing conduits, electrical boxes, switches, and other components. It ensures accurate alignment and levelness of these elements, which is crucial for proper installation and a neat, finished result.
Besides levelling tasks, torpedo levels can also be used for determining slopes and angles, making them versatile tools in various electrical applications.
Choose a torpedo level that is easy to hold and use. Comfortable handling is essential when working in tight spaces or overhead positions, allowing you to achieve accurate readings without strain.
Many electricians prefer torpedo levels with magnetic sides as they offer added practicality. The magnetic feature allows you to easily attach the level to metallic surfaces, freeing up your hands for adjustments and ensuring a hands-free levelling experience. Invest in a high-quality torpedo level that can withstand the demands of daily electrical work. Durable materials and construction ensure the tool's longevity and reliable performance.
Regularly inspect and clean your torpedo level to keep it accurate and free from debris. Store it securely in your tool kit to prevent damage and ensure easy accessibility when needed.
FISH TAPE
Fish tape, also known as draw wire or ‘electrician’s snake’, is a flexible and flat tool used for pulling wires or cables through conduits, pipes, or walls. Electricians often use fish tape to route and guide electrical wires during installations, especially when working in confined spaces or existing structures.
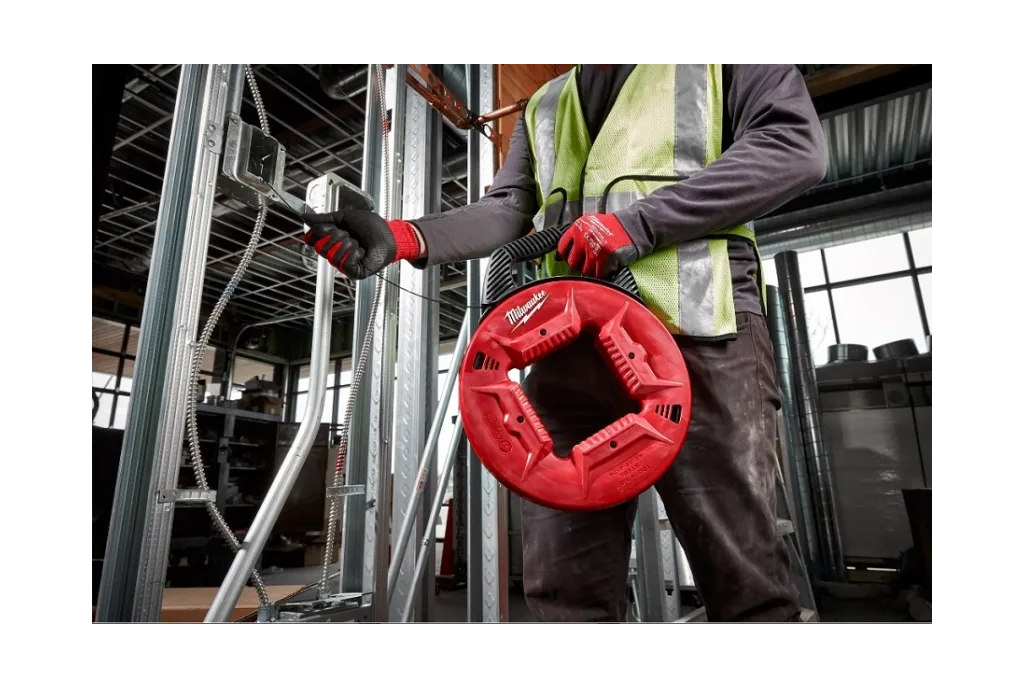
Fish tapes are typically made of steel or fiberglass and can be coiled or uncoiled as needed for specific tasks. They are usually housed in a retractable coil and can be fed through installed conduit piping.
DEBURRING TOOL
Deburring tools are used to remove sharp edges or burrs from the cut ends of pipes, tubes, or other materials after they have been cut. Burrs can be formed during cutting processes and need to be removed to ensure smooth and safe connections.
Deburring tools come in various shapes and sizes, and they are essential for creating clean and precise openings for fittings and connections.
PIPE REAMERS
Pipe reamers are tools used to enlarge and shape the end of a pipe or tube to make it suitable for fitting into connectors or other pipe ends. They are often used to remove any irregularities or roughness from the pipe ends, ensuring a proper and secure fit with other pipe components.
Pipe reamers can be hand-operated or powered, and they come in various sizes to match different pipe diameters.
DUCT RODS
Rods, or duct rods, are stiff and flexible rods used for cable and wire pulling in underground ducts or conduits. They are commonly made of fiberglass or other sturdy materials. Electricians and telecom technicians use rods to navigate through long and tight cable paths, making it easier to route cables and wires accurately in buried or hidden areas.
TAPE MEASURE
A tape measure is another important item in your toolkit. Electrical installations and repairs require precise measurements for cutting, positioning, and aligning various components. A tape measure ensures accuracy in measurements, leading to efficient and professional-quality work.
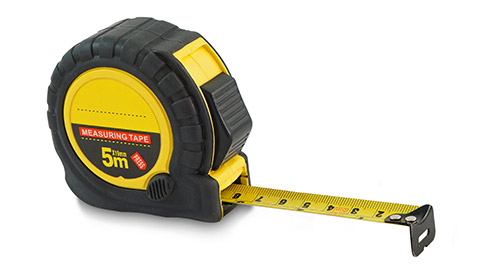
Choose a heavy-duty tape measure that can withstand the rigors of daily use in demanding electrical environments. Consider a tape measure with a magnetic tip, as it facilitates one-handed use when measuring metal components or working in tight spaces. A belt clip on the back allows for easy and quick access, keeping the tape measure within reach at all times.
Familiarise yourself with different measuring techniques, such as reading fractions and converting between metric and imperial measurements, to become proficient in using the tape measure effectively.
Watch this video to check your measuring skills.
Activity
Check how good your measuring skills are by completing this activity. When you are done, save it as a pdf. You can bring it to class to check with your classmates and tutor.
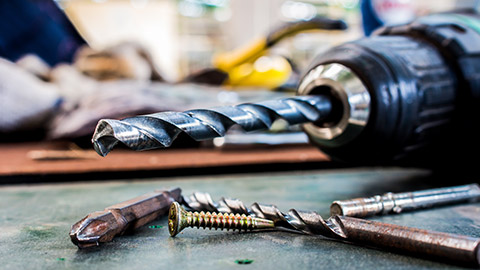
What we're covering:
- Power tools – drills (impact, hammer, joist & stud, Hole Hawg, rotary hammer), drill bits.
Power tools
Watch the following videos which discuss the essential power tools for electricians.
(Be aware some these power tool videos may be sponsored by manufacturers, so focus on learning the tool functionalities and techniques without being influenced too much by brand promotions.)
- Top 7 Power Tools EVERY Electrician Should Have
- 7 Power Tools Every Electrician Needs
- 10 Power Tools ELECTRICIANS SHOULD HAVE
You will need the right power tools to perform your job with accuracy and efficiency. From installing electrical equipment on different surfaces, ranging from soft materials like wood to the toughest ones like concrete, metal, and masonry, to cutting wires and cables, you require a versatile set of corded and cordless tools to get the job done safely and effectively.
POWER DRILLS
A power drill, also known as a standard drill or electric drill, is a versatile handheld tool used for drilling holes in various materials, such as wood, metal, plastic, and masonry. It operates by rotating a drill bit to create holes, and the speed can be adjusted based on the material being drilled.
Power drills are suitable for general drilling tasks and driving screws or fasteners, making them a versatile choice for a wide range of projects. They also used to create holes for running cables, mounting electrical boxes, and attaching fixtures.
Power drills can be corded, requiring a power outlet, or cordless, powered by rechargeable batteries. They come in various sizes and power ratings to suit different tasks.
A cordless drill is a type of power drill that operates on rechargeable batteries, offering greater portability and flexibility compared to corded drills. Cordless drills are widely used by electrical workers for tasks in areas without easy access to power outlets, providing freedom of movement during installations and repairs. Cordless drills may be referred to as battery drills. Stocking up your toolbox with spare batteries and a drill bit set with different sizes is highly recommended.
While drills are versatile tools, a single drill may not be able to handle all the duties you want it to. Different types of drills serve specific purposes and excel in various applications. Here's a summary of what each type of drill is best suited for:
IMPACT DRILL
An impact drill, also known as an impact driver, is a high-torque tool designed to fasten screws into wood, metal, and other materials during installations and repairs. It delivers a lot of rotational force, particularly at low speeds, making it excellent for heavy-duty tasks. They are not typically used for drilling holes.
Impact drills are available in both corded and cordless models, with the cordless versions offering greater mobility. Additionally, impact drills are smaller and more compact than traditional drills, which adds to their portability and ease of use. They also tend to be lighter in weight, reducing user fatigue during extended use.
HAMMER DRILL
A hammer drill is a powerful tool that combines standard rotary drilling with a forward and backward hammering action, allowing it to drill into stone, concrete, or other masonry more effectively.
Electrical workers use hammer drills for drilling holes into concrete walls, brickwork, and other tough surfaces when installing electrical fixtures. Hammer drills are available in both corded and cordless models.
COMBINATION DRILL/DRIVER KITS
Combination drill/driver kits often come with both a standard drill and an impact driver, which offers versatility for drilling and fastening tasks. With the power drill, you can drill holes in various materials like wood, metal, and plastics, while the impact driver is excellent for driving screws and fasteners with high torque.
The kit is an ideal choice starting out as it covers a wide range of common tasks.
Even with a combination kit, there may still be tasks that require other specialised drills. Having a power drill and an impact driver as part of a combination kit is a good starting point, and then adding a hammer drill or rotary hammer for masonry work and a joist and stud drill for tight spaces can enhance the versatility of the toolset.
JOIST AND STUD DRILL /RIGHT-ANGLE DRILL
A joist and stud drill, also known as a right-angle drill, features a 90-degree angled chuck, allowing it to reach tight spaces and corners that standard drills cannot access easily. It is primarily designed for drilling holes in confined areas, such as between studs, joists, or other obstacles. Electricians use joist and stud drills to drill holes in tight spaces when running electrical cables or conduits through walls or ceilings.
HOLE HAWG
A Hole Hawg is a heavy-duty and high-torque drill designed for drilling large holes in wood and other materials. It typically has a two-handed design for added control and stability. Electrical workers commonly use Hole Hawgs for drilling larger holes for conduit installations and cable pass-throughs. These are great when you’ve got 4 or more studs stacked together and you need to drill a hole through all of them to feed a wire through.
ROTARY HAMMER DRILL
A rotary hammer is a heavy-duty tool designed for drilling into hard materials like concrete, stone, and masonry. It uses a piston mechanism to deliver hammer blows in addition to rotation. Electrical workers use rotary hammers for demanding tasks that require drilling large and deep holes in concrete during installations and structural work.
DRIVERS AND DRILLS
A driver and a drill are handheld power tools with distinct purposes. A driver is designed for driving screws, offering adjustable torque settings and features like LED lights. It uses screwdriver bits in a hexagonal or square chuck. On the other hand, a drill is meant for drilling holes, equipped with adjustable speed settings and a keyless chuck for various drill bits. While drills can drive screws, they lack the torque control of drivers. In essence, a driver is for screws, providing torque control, while a drill is for drilling holes, offering variable speed control.
DRILL BITS
You might be surprised how often you need to drill a hole. Ensure you aways have a decent set of twist bits on hand.
Drill bits are tools used to create holes in various materials. They are typically made from high-speed tool steel, which is hard but brittle. To effectively cut into a work surface, the drill bit material needs to be harder than the material being drilled.
There are different types of drill bits to suit various applications and materials. In the electrotechnology industry, some commonly used drill bits include:
TWIST DRILL
This is the most common type of drill bit. It has spiral-shaped flutes that act as cutting edges and help carry away shavings while providing a path for lubricant to the cutting edge.
The drill also has specific cutting angles, clearance angles, and rake angles.
AUGER BIT
Used for drilling into both hard and soft wood, the auger bit features a spiral shape and is effective in creating clean holes.
SPADE BITS (SPEED BORES)
An alternative to auger bits for wood, spade bits have a flat, paddle-like shape and can cut into hard or soft wood with ease.
MASONRY DRILL BITS
These bits have tungsten carbide points, which enable them to cut through concrete without losing their shape.
The body of the bit is heat-treated to prevent compression and allow the power drill's hammer action to efficiently transfer energy to the concrete.
STEP DRILL BITS
Step drill bits, also known as unibits or cone drill bits, are a specialised type of drill bit used for drilling holes in various materials, particularly sheet metals. These bits have a unique design with multiple stepped, conical cutting edges which allows the bit to drill progressively larger holes without the need to change bits or switch to different sizes.
Step drill bits are especially useful when drilling holes in thin materials or when precise hole sizes are required. One significant advantage of this bit is its ability to create smooth, burr-free holes.
FORSTNER BITS
Forstner bits are often used by electricians for drilling flat-bottomed holes, especially in wood. They are ideal for creating clean, precise holes and are commonly used for installing electrical outlets and switches in wooden surfaces.
Drill bits with a diameter of less than 12.8mm, typically have a parallel shank that allows them to be held in a three-jaw Jacobs chuck on the drilling machine, enabling them to be spun at the appropriate speed and fed into the work surface.
DRILL SPEEDS
Drill speeds are determined by the cutting speed, which refers to the speed at the outside edge of the tool, also known as surface speed. It is measured in meters per minute (m/min). If two tools of different sizes are running at the same revolutions per minute (rpm), the larger tool will have a higher surface speed.
The cutting speed depends on two main factors: the type of material being cut and the type of cutting tool being used. Additionally, the hardness of the work material plays a significant role in determining the recommended cutting speed. Using too high a cutting speed can generate excessive heat and potentially damage the drill bit.
As a general rule, when working with harder materials, it is advisable to use a slower cutting speed. Conversely, when dealing with softer materials, a faster cutting speed can be used to achieve optimal results. Finding the right balance between cutting speed, material hardness, and the type of cutting tool is crucial for efficient and precise drilling operations.
Activity
Activity
Review all the information about drills and then have a go at this question:
Calculate the cutting speed for a drill bit with a diameter of 8mm and a rotational speed of 1200 revolutions per minute (rpm).
The cutting speed formula is:
Cutting Speed (m/min) = π × Diameter (mm) × Rotational Speed (rpm) / 1000.
Ask your tutor to check your answer next time you are in class.
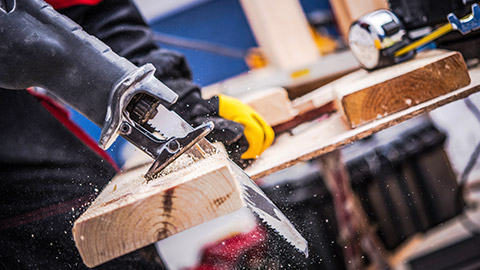
What we're covering:
- Power tools – electric saws (reciprocating, circular, jigsaw, bandsaw), cordless screwdrivers
This content continues the learning on power tools that started in the previous session.
ELECTRIC SAWS
Based on what job you are doing, there are several types of electric saw available, each with specific qualities to help you carry out your tasks efficiently.
RECIPROCATING SAW
A reciprocating saw, also known as a Sawzall, is a powerful handheld tool with a back-and-forth cutting motion. It is suitable for cutting through various materials, including wood, metal, plastics, and drywall.
Electrical workers use reciprocating saws for demolition work, cutting conduit, removing old fixtures, and making rough cuts when running wires.
Reciprocating saws come in both corded and cordless variants. Cordless models offer more flexibility in tight spaces.
CIRCULAR SAW
A circular saw is a versatile handheld power tool equipped with a rotating blade, specifically designed for making straight cuts in materials such as wood, plywood, and MDF. Electric workers find circular saws extremely useful for cutting lumber, plywood, and other materials during construction and installations. These saws are available in both corded and cordless versions, with cordless models being particularly convenient for jobs without access to power outlets.
For those in the construction side of the trade, a circular saw is an indispensable tool. It may not be commonly used by service electricians, but anyone working in a wood-framed environment will greatly benefit from having one. This tool is frequently employed for ripping down studs, crafting scabs, or creating braces for light fixtures. While a Sawzall can serve this purpose as well, when multiple cuts need to be made quickly and efficiently, a circular saw proves to be the superior choice.
JIGSAW
A jigsaw is a versatile power tool equipped with a reciprocating blade that moves up and down, making it ideal for creating curved and intricate cuts in various materials.
Electric workers find jigsaws useful for cutting holes in drywall, making notches for conduits, and fitting electrical boxes into walls.
Jigsaws are available in both corded and cordless models, with the cordless versions offering more manoeuvrability and convenience in situations where access to power outlets may be limited.
BAND-SAW
Band saws are useful tools due to their efficiency in cutting metal conduit and strut. When electricians frequently deal with cutting metal materials, having a band saw proves more practical than relying solely on a Sawzall for all cutting tasks.
Band saws offer cleaner cuts compared to Sawzall, resulting in neater and more precise work. Another advantage of band saws is the longevity of their blades, which tend to last much longer than Sawzall blades.
Activity
Read the two scenarios following, then answer the accompanying questions. Post them on the class forum and read and comment on what your classmates write.
Scenario 1
You are an electrical worker tasked with installing conduit in a construction site. You need to cut through metal conduit using an electric saw.
- Identify the type of electric saw you would use for cutting metal conduit.
- List three specific safety precautions you should take before using the electric saw.
- Describe how you should position yourself and the conduit while using the saw to ensure safety.
- Explain why it's important to choose the appropriate blade for cutting metal conduit.
Scenario 2
You are working on a residential electrical installation project. You need to create precise holes in drywall to install electrical boxes.
- Which type of electric saw would you choose for this task? Explain your choice.
- List two safety precautions you should take before using the selected electric saw in this scenario.
- Describe how you would ensure accurate and controlled cuts in the drywall.
- Why is it important to wear safety goggles when using an electric saw?
CORDLESS SCREWDRIVERS
Electric screwdrivers, commonly known as cordless screwdrivers or battery-powered screwdrivers, are designed for driving screws and small fasteners with ease. Electrical workers rely on them for repetitive screw-driving tasks, such as securing electrical components and covers.
These compact and lightweight tools come in various sizes and torque settings, making them suitable for different screw sizes and applications. They can be either corded or cordless, providing flexibility based on the user's needs and preferences.
A high-quality electric screwdriver should be lightweight, anti-shock, and ergonomic, ensuring minimal strain and enhanced productivity during extended use. Safety features are essential to prevent accidents and injuries while handling the tools.
To accommodate different types of screws and materials, electric screwdrivers come with flexible speed ranges. Additionally, they are equipped with LED lights, enabling users to work efficiently in dark and dimly lit areas. For cordless models, fast charging systems are incorporated to minimise downtime and maintain optimal productivity.
Activity
Activity
Congratulations! You've just won a $1500 voucher to spend on tools that will kickstart your journey as an electrical worker. Imagine you're going on a shopping spree to create the ultimate toolkit. With this voucher in hand, carefully select the tools you would purchase to best suit your needs as you start out in the electrical field.
Your task is to create a list of tools you would buy with the $1500 voucher. Keep in mind the type of electrical work you plan to pursue (residential, commercial, industrial), the tasks you'll encounter, and the tools that will enhance your efficiency and safety.
For each tool note the:
- Tool Category - List the type/category of the tool.
- Tool Name - Specify the name of the tool.
- Reason for Selection - Explain why you've chosen this tool and how it will be valuable in your work.
- Estimated Cost - Provide an estimated cost for each tool.
- Total Cost - Calculate the total cost of all the selected tools.
Repeat the same format for each tool you'd like to include in your toolkit. Once you've completed your shopping list, you'll have a clear picture of how to maximize your $1500 voucher to create a comprehensive toolkit tailored to your specific needs as you embark on your electrical career.
You have three days to complete your shopping list and upload it to the class forum for discussion with the group. You may consider using a table or spreadsheet to streamline the presentation.
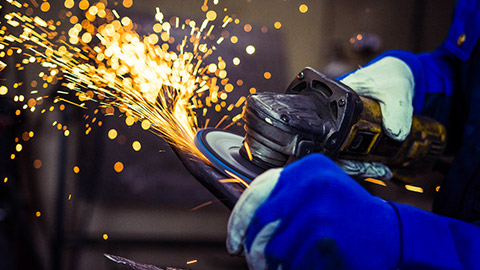
What we're covering:
- Power tools – angle grinders, wall chasers, bench grinders, rotary tool, heat gun.
The content in this session continues from the previous two lessons on Power Tools.
ANGLE GRINDERS
An angle grinder is used for cutting and grinding metal, masonry, and other materials. Electrical workers use angle grinders for cutting conduit, metal plates, hardy board, and removing rust or paint from metal surfaces. Angle grinders are available in different sizes and power options. They can be corded or cordless, with corded models providing more power for heavy-duty tasks.
WALL CHASERS
Wall chasers are essential power tools used by electricians for installing wires in walls. They are designed with twin blades that create narrow channels in the walls to accommodate cables and conduits.
These tools save significant time and effort as they allow clean and accurate cutting of grooves and channels in walls. Wall chasers are powered by electric motors that drive electric discs, similar to those found in angle grinders. For a dust-free working environment, wall chasers with a vacuum cleaner connection are highly desirable as they effectively collect the generated dust during operation.
Qualities to Look for in Wall Chasers:
- Lightweight and Ergonomic Design: The best wall chasers should be light in weight to minimise operator fatigue during extended use. An ergonomic D-shape handle further enhances user control, especially during heavy-duty operations.
- Special Guards for Chip Ejection: To ensure secure work, wall chasers should come equipped with special guards that prevent chip ejection while working. This feature contributes to the safety of the operator and surrounding areas.
- Advanced Channel Width and Cutting Depth Adjustments: Wall chasers should offer advanced adjustments for channel width and cutting depth. This versatility allows them to perform various operations effectively and efficiently.
BENCH GRINDERS
Bench grinders are versatile power tools commonly used for various tasks related to metalwork and sharpening tools. They consist of a motor-driven grinding wheel mounted on a sturdy workbench, providing stability and precision during use.
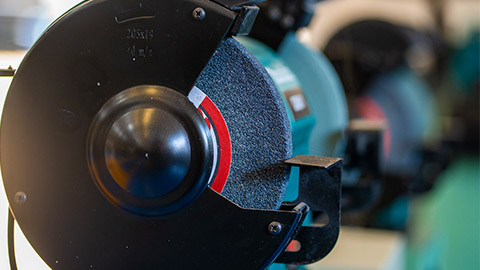
For electricians, bench grinders serve multiple purposes and offer several benefits:
- Tool Sharpening: Electricians use a wide array of hand tools, such as screwdrivers, pliers, and wire strippers. Bench grinders are ideal for sharpening these tools, restoring their cutting edges and functionality.
- Deburring and Cleaning: A bench grinder with a wire wheel attachment can quickly remove burrs or rough edges on metal components, ensuring smooth and safe installations.
- Metal Shaping: Bench grinders equipped with grinding wheels of different grits can be used to shape and modify metal surfaces as required.
- Removing Rust and Paint: Bench grinders, especially with a wire wheel or a sanding disc attachment, are excellent for removing rust and old paint from metal surfaces.
- Cutting and Polishing: Some bench grinders come with cutting or polishing attachments, allowing electricians to cut metal rods or polish finished metalwork for a professional appearance.
- Precision Work: The stable platform of a bench grinder enables precise control during grinding, making it suitable for delicate tasks that require accuracy, such as shaping small metal parts or sharpening fine tools.
It is crucial to observe safety practices and use the bench grinder with care to prevent accidents and injuries. Always wear appropriate personal protective equipment, such as safety goggles and gloves, to safeguard against sparks and debris. Ensure the workpiece is securely clamped to prevent accidents and maintain control during grinding. Avoid excessive pressure on the grinding wheel to prevent overheating and premature wear.
ROTARY TOOL (DREMEL)
A rotary tool, commonly known as a Dremel, is a handheld tool with various attachments, such as grinding wheels and cutting discs, for precision work. Electrical workers use rotary tools for tasks like grinding, polishing, and cutting small items or making precise modifications to electrical components. Rotary tools come in corded and cordless variants, with cordless models offering better mobility.
HEAT GUNS
A heat gun is a handheld tool that emits a stream of hot air. It is used for various applications, including stripping paint, soldering, and shrinking heat shrink tubing.
Electrical workers use heat guns for tasks like soldering wires, removing heat-shrink tubing, and bending plastic conduits. Heat guns can be corded or cordless, with adjustable temperature settings.
Activity
Complete this activity to consolidate your knowledge of power tools. Save your work as a resource for your own learning.
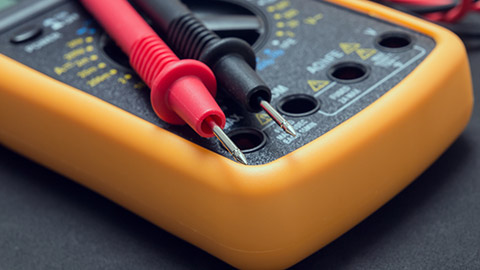
What we're covering:
- Meters and testers - multifunction, voltage tester, IR, multi-meter, clamp-on ammeter, phase rotation, circuit finders, line locators.
- AS/NZS 3017:2022 AS/NZS 3760:2022
The scope of electrical work you engage in, as well as the testing requirements, will determine the specific type of test equipment you will need in your tool kit.
Remember that after checking an electrical installation visually, tests should be carried out in accordance with AS/NZS 3000:2018, Clause 8.3.3. These tests make sure the installation meets the standard requirements and is safe for its intended use.
You must adhere to the Electricity (Safety) Regulations, ESR 63 and ESR 90, which mandate testing for all prescribed electrical work on installations and appliances and in order to perform these tests effectively, you must possess suitable and compliant test equipment.
AS/NZS 3017:2022 is a guide for inspecting and testing low voltage electrical setups. It ensures they comply with safety rules to prevent fires and protect people and animals from electric shocks. This guide applies to installations connected to an MEN system. Use AS/NZS 3017:2022 to meet the Periodic Verification needs of both the Electricity (Safety) Regulations 2010 and AS/NZS 3019:2007. It contains helpful checklists for visual inspection and testing, which electricians should keep handy. By using these checklists along with AS/NZS 3000:2018, you can ensure electrical setups are safe and meet the standards.
Selecting the right test equipment:
- Assess Your Testing Needs: Consider the specific tests you will need to conduct. Understanding your requirements will help you make informed decisions when choosing the appropriate equipment. (See the table below.)
- Conduct Research: Before making any purchases, conduct thorough research. Seek advice from experienced electrical practitioners and explore various suppliers of testing equipment. Evaluate whether a particular meter is fit for your intended purpose, ensuring it offers accuracy, appropriate overvoltage category rating (cat rating), suitable resolution, test values, and the required ranges.
- Comprehend Specifications: Review the specifications of potential test equipment. If you don't understand some of the technical jargon, seek guidance from someone knowledgeable in the field. Understanding these specifications is crucial to selecting the right tools.
- Choose Reputable Brands: Select reputable and reliable brands known for producing robust, good-quality equipment. Additionally, look for products that come with after-sales warranties, providing you with added assurance.
The following table, created by the Electrical Workers Registration Board summarises the types of test instrument required for various measurements:
Testing Instrument measuring | ||
---|---|---|
Voltage AC and DC | Dedicated voltage tester. | Should be capable of reading all working voltages, both AC&DC. |
Resistance | 500V DC Insulation resistance (IR) tester or incorporated in multifunction tester. | For testing a 400V 3 phase or 230V single phase installation a 500V DC test voltage is required as a minimum. |
Resistance | Multi-meter or incorporated in multifunction tester. | Multi-meter should be rated Cat III. |
Current | Clamp-on Ammeter. | Cat III clamp-on ammeter capable of reading all load requirements. |
Leakage Current | Leakage current clamp-on Ammeter. | Cat III high resolution clamp-on ammeter capable of milliamps. |
Fault Loop-Impedance | Incorporated in multifunction tester. | Cat III or IV. |
RCD Testing | Incorporated in multifunction tester. | Capable of 30mA and 10mA RCD tests. |
Phase Rotation | Phase rotation tester. | Contactless meter offers more safety. |
MULTIFUNCTION TESTER
Multifunction testers are widely available from major electrical test equipment manufacturers. You can easily find information about different brands and models by searching online or asking electrical wholesalers for guidance.
The main advantage of multifunction testers is that they combine multiple testing functions in one device. This makes it efficient for electrical workers to perform all the necessary tests required to meet AS/NZ Standards and regulations. It simplifies the testing process and is useful for various electrical tasks.
While multifunction testers can do many tests, it's also helpful to consider having separate specialised tools for specific tasks. This can improve precision and efficiency, especially for complex projects. Having separate instruments can act as a backup in case one fails, ensuring work continues without interruptions. Additionally, using separate meters for different jobs can boost productivity, enabling multiple tasks to be done simultaneously. This is particularly useful for bigger projects or when multiple teams are working together.
Some of the key functions performed by multifunction testers include:
- Insulation Resistance Testing: This test measures the resistance between conductive parts and the earth, ensuring the effectiveness of insulation in electrical circuits and identifying potential leakage paths or insulation breakdowns.
- Earth Loop Impedance Testing: Earth loop impedance testing evaluates the impedance or resistance of the earth connection in the event of a fault, ensuring that fault currents can be safely discharged, minimising the risk of electric shock.
- RCD (Residual Current Device) Testing: RCDs are critical safety devices that protect against electric shocks by rapidly disconnecting the power supply during a fault. Multifunction testers can verify the proper functioning and safety limits of these devices.
- Polarity Testing: Polarity testing checks the correct connections of live, neutral, and earth conductors in an electrical system. Proper polarity ensures that electrical appliances and equipment function as intended, reducing the risk of electrical faults.
- Continuity and Resistance Measurement: Multifunction testers can measure continuity and resistance in electrical circuits, helping to detect loose connections, faulty wiring, or damaged components.
- Voltage and Current Measurement: These testers can also measure voltage and current in both AC and DC circuits, providing valuable information about the electrical system's performance.
- Phase Sequence Testing: In three-phase electrical systems, a multifunction tester can determine the correct sequence of phases, ensuring that motors and machinery run in the intended direction.
- Data Logging and Reporting: Many multifunction testers come equipped with data logging capabilities, allowing electricians to store test results for analysis and documentation. Detailed reports can be generated for compliance and regulatory purposes.
- Frequency and Capacitance Measurement: Some advanced multifunction testers offer additional functions, such as measuring frequency and capacitance, providing more comprehensive insights into electrical systems.
DEDICATED VOLTAGE TESTER
A voltage tester is a handheld device used to quickly check if a circuit or appliance is energised, before working on it. The simplest and safest type of voltage tester is the non-contact voltage tester, powered by batteries, which can detect electricity by being close to an outlet slot or wire.
It is essential to use a voltage tester to detect AC voltages on sockets, switches, outlets, and circuit breakers before commencing an electrical project.
The voltage tester's indicator, often a light-emitting diode (LED), illuminates if voltage is present, indicating the need to shut down the current before starting work. This is a vital safety measure required by health and safety legislation.
INSULATION RESISTANCE (IR) TESTER
An Insulation Resistance (IR) Tester is a specialised test instrument used to evaluate the integrity of insulation in electrical systems. The primary purpose of this tester is to detect insulation leakage between live conductors and between live conductors and earth. It helps electricians and electrical professionals identify potential faults, weaknesses, or breakdowns in the insulation of electrical circuits and appliances. It works by applying a test voltage to the circuit being examined and measuring the resistance of the insulation.
Regularly conducting insulation resistance tests is essential for maintaining the reliability and safety of electrical installations. Electricians often use the IR tester during maintenance, troubleshooting, and safety inspections to ensure that insulation is performing as expected. When using the IR tester, proper safety precautions must be followed, including de-energizing the circuit before performing the test.
According to AS/NZS 3000:2018 8.3.6.1, the IR tester must maintain the terminal voltage within +20% and -10% of the nominal open circuit voltage while measuring a resistance of 1 MΩ on the 500V range or 10 MΩ on the 1000V range.
MULTI-METER
A multimeter is a versatile digital tool combining multiple functions into a single device. It can read a wide range of electrical parameters, including:
- Voltage: Multimeters can measure both AC (alternating current) and DC (direct current) voltage. They are used to determine the potential difference between two points in an electrical circuit.
- Current: Multimeters can measure both AC and DC currents flowing in a conductor. They allow electricians to determine the amount of current passing through a circuit.
- Resistance: Multimeters can measure the resistance of an electrical component or circuit. Resistance refers to the opposition of current flow in a conductor.
- Continuity Testing: Multimeters can check for continuity, which determines if a circuit is complete and capable of conducting electricity. It is often used to identify open circuits or faulty connections.
- Diode Testing: Some multimeters have a diode testing function, which helps check the health of diodes in electronic circuits.
- Capacitance: Advanced multimeters can measure capacitance, which determines the ability of a component to store an electrical charge.
- Frequency: Certain multimeters can measure the frequency of an AC signal, which is the number of cycles per second.
- Temperature: Some multimeters come with temperature measurement capabilities, often using a thermocouple probe.
- Duty Cycle: Duty cycle measurement allows you to assess the percentage of time a digital signal is high (on) compared to the total period.
- Non-Contact Voltage Detection: Some multimeters have a non-contact voltage detection feature, which allows them to detect the presence of AC voltage without making direct contact.
CLAMP-ON AMMETER
Clamp-on ammeters are non-invasive electrical testing instruments used to measure AC and DC currents without disconnecting wires. They are similar to a standard tester or multimeter with the addition of a clamp/jaw that reads amperage on large diameter conductors. They offer a wide range of current measurement capabilities, and many models come with additional functions like voltage, resistance, frequency, and capacitance measurements. They are widely used in various industries for electrical maintenance, troubleshooting, and inspections. Proper safety precautions and regular calibration are essential for accurate and reliable readings.
PHASE ROTATION METER
Phase rotation meters, also known as phase sequence testers, are specialised electrical testing instruments used to identify the correct sequence of phases in a three-phase system. This is essential for ensuring the proper operation of motors, machinery, and other three-phase equipment.
Phase rotation meters often use non-contact testing methods, making them safe and easy to use. They can determine phase sequence without the need for physical contact with live conductors.
Many phase rotation meters feature LED indicators that display the correct phase sequence. These indicators may use arrows or numbers to show the proper sequence of phases. Some phase rotation meters also have audio indicators, such as buzzers or beeps, that provide an additional way to detect the phase sequence.
Phase rotation meters are suitable for both low-voltage and high-voltage applications, making them versatile tools for various electrical systems.
In addition to identifying phase sequence, phase rotation meters can also be used to test the rotation direction of three-phase motors, ensuring they are connected correctly.
Most phase rotation meters are portable and handheld, allowing electricians and technicians to easily carry them to different job sites.
CIRCUIT FINDERS
Circuit finders, also known as circuit tracers or circuit breakers finders, are used to locate the path of live electrical circuits in walls, ceilings, or floors. They are particularly useful for finding circuit breakers, tracing wiring paths, and locating electrical faults in complex wiring systems.
Circuit finders work based on the principle of electromagnetic field detection. When an electrical current flows through a conductor, it generates a magnetic field around it. The circuit finder's transmitter unit is connected to the electrical circuit or breaker panel. It injects a signal into the circuit, which creates a magnetic field along the path of the live wires. The handheld receiver unit is then used to detect the magnetic field and trace the path of the live wires, allowing electricians to identify the course of hidden electrical lines.
LINE LOCATORS
Line locators, also called line tracers or underground cable locators, are used to locate underground or buried electrical cables, pipes, or other conductive materials before excavation or construction work, preventing accidental damage to buried utilities. They work based on the principle of electromagnetic induction. When an alternating current is applied to an electrical cable, it generates an electromagnetic field around the cable.
The line locator's transmitter unit applies an alternating current to the cable, creating an electromagnetic field that radiates outward. The handheld receiver unit is then used to detect the electromagnetic field and pinpoint the location of the underground cable, allowing electricians to trace its path without digging.
A Final Word about Test Equipment Selection…
When choosing an electrical test instrument, it is essential to prioritize safety and ensure the meter is suitable for the intended use. Here are some key steps to follow:
- Understand Measurement Categories: Begin by identifying the measurement categories (Cat II, Cat III, Cat IV) suitable for your specific tasks. This ensures that the test instrument is appropriate for the electrical environment it will be used in.
- Verify Electrical Safety Standards: Look for the correct electrical safety standard applicable to the test instrument you need. Ensure it complies with the relevant safety regulations to guarantee safe operation.
- Seek Independent Type Testing: Check if the test instrument has undergone independent type testing to the safety standard mentioned. This provides assurance that the meter meets safety requirements and has been rigorously tested.
- Check Warning Labels and Markings: Inspect the test instrument for warning labels or markings that indicate its safe use, potential hazards, and operating instructions. Adhere to these instructions to prevent accidents or damage.
- Review Specifications: Examine the meter's specifications to assess its performance capabilities objectively. Pay close attention to accuracy, resolution, range, and precision, considering all these factors together to make an informed decision.
- Ensure your test instruments undergo annual testing and recalibration by an approved supplier to maintain their accuracy at an acceptable level. It's crucial that your test instrument carries a calibration certificate; otherwise, recorded results may become invalid.
- To keep your meter operational and safe, periodically verify its accuracy. For common (non-specialist) meters used in regular installation work, routine accuracy checks of calibration are straightforward and quick. It's highly recommended to perform these checks regularly and document the results. However, if you find that the meter is out of calibration, you should send it to an accredited laboratory for correction. These routine checks are not a substitute for accredited calibration.
AS/NZS 3760:2022 – Ensuring electrical safety through in-service inspection and training
Introduction
AS/NZS 3760:2022 plays a vital role in promoting electrical safety and compliance with regulations in Australia and New Zealand. This standard serves as the foundation for testing and tagging electrical equipment, with a strong emphasis on ensuring user safety.
Scope and Applicability
AS/NZS 3760:2022 is applicable throughout the lifecycle of electrical equipment. It addresses situations when equipment is put into service for the first time, in use, available for second-hand sale or hire, or has undergone servicing or repair. This latest version focuses on inspection and testing guidelines for Class I and Class II appliances, functional earthing, insulation, leakage current, RCD tripping times, cord sets, and earth continuity resistance.
Safety Focus
The primary objective of AS/NZS 3760:2022 is to guarantee the safety of electrical equipment used in diverse settings, including workplaces, homes, and public spaces. The standard outlines a systematic approach to inspecting and testing electrical equipment, aiming to identify defects, damage, or wear that could lead to unsafe conditions. By concentrating on safety concerns, AS/NZS 3760 ensures that equipment remains electrically sound and properly connected, minimising the risks of electric shock and fire hazards.
Inspection and Testing Procedures
AS/NZS 3760:2022 outlines comprehensive testing procedures, including visual inspections, insulation resistance tests, earth continuity tests, and polarity tests. These measures serve to assess the equipment's condition and its ability to prevent hazards effectively. The standard's emphasis on visual inspections, which can detect over 90% of defects, accounts for environmental hazards and the equipment's wear during testing.
Frequency of Inspections
The recommended inspection and testing frequencies within AS/NZS 3760:2022 are contingent upon equipment type, intended use, and environmental conditions. Regular inspections and testing are crucial in identifying and rectifying potential issues before they escalate into more serious safety risks.
Record Keeping and Compliance
AS/NZS 3760:2022 necessitates the maintenance of records detailing testing outcomes, including the tester's name, testing date, results, and the next scheduled testing date. This record-keeping system ensures accountability and traceability, contributing to overall compliance with safety regulations.
Role in Workplace Safety
AS/NZS 3760:2022 assumes a pivotal role in workplace safety by overseeing the Test and Tag industry regarding portable appliance electrical safety. It sets recommendations for testing various types of electrical equipment commonly found in workplaces, emphasizing test and tag frequencies, inspection and testing specifications, and record-keeping guidelines.
Activity
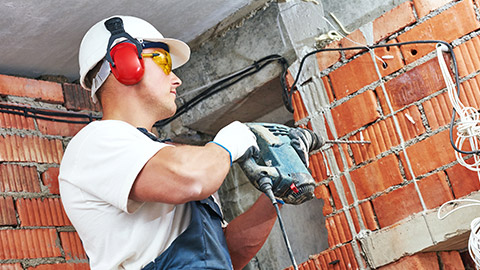
What we're covering:
- Personal Protective Equipment Potential hazards associated with power tool and appropriate PPE.
Power tools are widely used to perform tasks efficiently and effectively. However, using power tools involves inherent risks, especially when working with electricity. Identifying appropriate Personal Protective Equipment (PPE) and electrical safeguards is crucial to ensure the safety of operators and those nearby.
Understanding power tool hazards
Before identifying PPE and electrical safeguards, it is important to recognize the potential hazards associated with power tool use:
- Electrical shock: Power tools connected to electrical sources can pose a risk of electric shock, leading to severe injuries or fatalities.
- Mechanical hazards: Moving parts of power tools, such as rotating blades, drills, or abrasive wheels, can cause cuts, abrasions, or amputations.
- Noise exposure: Many power tools generate high noise levels, leading to hearing damage or loss if not adequately protected.
- Vibration hazards: Prolonged use of power tools can result in hand-arm vibration syndrome (HAVS) or whole-body vibration-related health issues.
- Flying Debris: Some power tools, like drills and grinders, can produce flying debris that may cause eye injuries or lacerations.
- Kickback: Tools with rotating components, such as saws and grinders, can experience kickback if the blade binds or pinches, leading to loss of control.
- Dust and Fume Exposure: Cutting and grinding generate dust and fumes that can be harmful when inhaled, potentially causing respiratory issues.
- Burn Hazards: Heat guns can cause burns if users touch the hot nozzle or direct heat at their skin.
- Fire Hazards: Certain power tools, like heat guns and grinders, can generate sparks and ignite fires, especially when used near flammable materials.
- Over-tightening: Cordless screwdrivers pose a risk of over-tightening screws, leading to damaged workpieces and potential accidents.
- Hand Strain: Prolonged use of power tools can cause hand and arm strain, leading to fatigue and musculoskeletal injuries.
Activity
Consider the hazards associated with the power tools covered earlier in this course. Complete the table in this worksheet, providing at least two hazards for each and a brief explanation. The first one has been done for you.
Identifying appropriate PPE for power tool use
Personal Protective Equipment (PPE) is the first line of defense against potential power tool hazards. It includes various protective gear and equipment designed to reduce the risk of injuries. Wherever possible equipment should be non-conductive materials and rated at or above the voltage being worked on.
Electrical PPE may include safety glasses, face shields, hoods, hard hats, hearing protection, electrical hazard rated safety shoes, insulating rubber gloves with leather protectors, insulated sleeves, and arc rated clothing, depending on the tasks.
Prior to wearing PPE, you should:
- Perform a PPE hazard assessment and determine the PPE needed to provide protection.
- Obtain training on the proper use of PPE for working on or near exposed energised parts.
- Inspect and test PPE to ensure the equipment is not damaged or defective.
- Ensure your PPE is clean and free of liquid stains, oils or greases, or debris.
Be sure to:
- Use PPE according to manufacturers’ requirements.
- Perform tasks wearing required PPE.
- Use ALL required PPE.
Eye and Face Protection
Nonconductive safety glasses or goggles with side shields should be worn to shield the eyes from flying debris or particles, dust, splashing substances, harmful gases, vapors, aerosols, and high intensity radiation from welding operations. Consider anti-fog coatings on safety goggles to prevent fogging, ensuring clear vision even in humid or cold conditions. This feature is particularly advantageous when working in confined spaces or areas with temperature.
Face shields or visors with the appropriate arc flash rating may be necessary for some electrical work. Safety glasses or goggles should be worn underneath face shields.
AS/NZS 1336:2014 EYE AND FACE PROTECTION - GUIDELINES
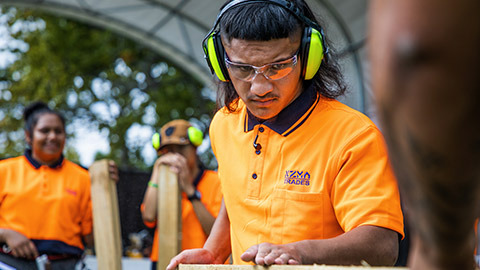
Provides recommended practices and guidance for the selection, care and use of eye and face protectors worn in occupational environments to protect eyes and faces against hazards, such as flying particles and fragments, and exposure to optical radiation occurring in industrial processes, such as welding.
HEAD PROTECTION
Nonconductive hardhats should be worn whenever there is a danger of head injury from electric shock or burns due to contact with live parts, being struck by flying or falling objects, or by striking one’s head against a fixed object.
AS/NZS 1801:1997 Head Protection Occupational protective helmets
This standard outlines the specifications for three types of protective helmets based on their intended use. It covers the construction of the helmet shell and finish, along with the testing methods. Furthermore, it includes specific additional performance criteria for occupational protective helmets used in high-temperature workplaces and for bushfire fighters' helmets, which are based on industrial helmets.
HEARING PROTECTION
When using noisy power tools, ear plugs, earmuffs or helmets with integrated hearing protection must be worn to prevent hearing damage. When selecting hearing protection, electricians should consider the Noise Reduction Rating (NRR) indicated on the product. The higher the NRR value, the better the protection from loud noises. It's essential to ensure the chosen hearing protection provides sufficient noise reduction for the specific power tools and workplace environment.
AS/NZS 1270:2002 Acoustics - Hearing protectors
This standard outlines the criteria for the design, material, and effectiveness of standard hearing protectors. It also offers guidelines for specialist hearing protectors and procedures to physically and acoustically test these devices.
HAND PROTECTION
Choose gloves based on the specific job requirements and potential hazards involved, balancing the need for cut resistance with other safety considerations, such as dexterity and protection against electrical hazards.
While non-conductive gloves are essential for electrical work involving live circuits, they might not be the most suitable option when using power tools. For power tool usage, prioritise gloves that offer protection against cuts, abrasions, and vibrations. Cut-resistant gloves are particularly important as they can safeguard against potential injuries from sharp edges, jagged sheet metal, and other hazardous objects encountered while working with power tools.
AS/NZS 2161.2:2020 Occupational protective gloves, Part 2: General requirements and test methods
This standard explains the general requirements and test methods for occupational protective gloves. It adopts the international standard ISO 21420:2020 but with some changes specific to Australia and New Zealand. The standard covers various aspects of protective gloves, including their design, construction, safety, comfort, and effectiveness. It ensures that gloves are safe to use, do not cause harm, and provide the intended protection for the hands.
RESPIRATORY PROTECTION
Respiratory Personal Protective Equipment (PPE) is essential for workers who use power tools in environments where airborne hazards, such as dust, fumes, and particles, are present. These hazards can arise from cutting, grinding, sanding, or other processes involving power tools.
The respiratory PPE is designed to protect the user's respiratory system from inhaling harmful substances that may cause respiratory issues or long-term health problems.
Types include disposable dust masks, half-face respirators, full-face respirators, and powered air-purifying respirators (PAPRs). Choose based on hazard type, filter efficiency, fit, comfort, and maintenance.
There are two standards covering personal respiratory protection and risk management. These standards form a basis for the selection, use and maintenance of RPE in Australian and NZ workplaces. When respirator use is required in the workplace, respirators shall conform to the requirements of AS/NZS 1716.
AS/NZS 1715:2009 Selection, use and maintenance of respiratory protective equipment. This standard offers information to employers and users on different types of RPE, how to select the right type for the job and how to correctly maintain it.
AS/NZS 1716:2012 Respiratory protective devices offer information to manufacturers, suppliers, employers and users by setting out performance requirements for different types of RPE.
FOOT PROTECTION
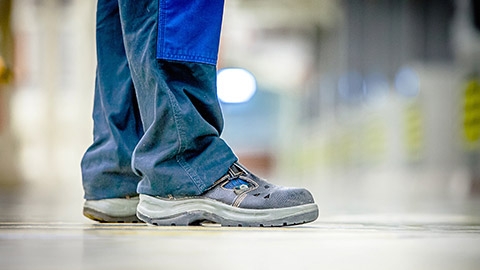
Foot protection is essential for electricians and other workers using power tools. Your feet are vulnerable to various workplace hazards, including falling objects, sharp materials, electrical shocks, or potential crushing incidents. Proper PPE ensures safety and prevents injuries in the workplace.
Types of Foot Protection include:
- Steel-Toed Boots: Have a reinforced steel cap in the toe area for protection against heavy objects and compression hazards.
- Composite-Toed Boots: Feature non-metallic toe caps and are lighter, suitable for electricians working in potentially energised environments.
- Electrical Hazard (EH) Rated Boots: Provide insulation against electric shocks with insulated soles and heels.
- Metatarsal Guards: Added protection for the metatarsal bones to safeguard against impacts and falling objects.
Properly fitted safety boots provide stability and reduce the risk of slips and falls while using power tools. They protect feet from impacts, falling objects, and sharp materials encountered while using power tools. Wearing appropriate foot protection also ensures compliance with workplace safety regulations.
AS/NZS 2210.3:2009 Occupational protective footwear - Specification for safety footwear specifies basic and additional (optional) requirements for safety footwear.
GENERAL BODY PROTECTION GEAR
General body protection gear will also safeguard against potential hazards when using power tools. Consider protective clothing such as: Overalls or long-sleeved shirts to shield the skin from sparks, hot materials, and chemical splashes during power tool usage and other electrical tasks.
Flame-resistant, non-conductive, natural fibre clothing when working with power tools near flammable materials or in high-heat environments to prevent burns.
Choose high-visibility vests to enhance visibility and safety, especially in low-light conditions or when working near moving vehicles.
KNEEPADS
Kneepads provide cushioning and support to protect the knees from impact and potential injuries caused by kneeling or crawling on hard surfaces.
They also help prevent long-term knee problems, such as joint pain and inflammation, arising from repetitive kneeling and bending.
FALL PROTECTION
When working with power tools at heights or on elevated surfaces, you must ensure you have the appropriate fall protection equipment in place. This includes wearing harnesses and using other safety gear such as belts, pole straps, supports, tennis elbow braces etc.
AS/NZS 1891.1:2020 Personal Equipment for Work at Height, Part 1: Manufacturing requirements for full body combination and lower body harnesses specifies requirements for the materials, design, manufacture, testing and marking of full-body, combination, and lower-body harnesses designed for working at height.
Activity
Matching Power Tool Scenarios, Hazards, and Correct PPE
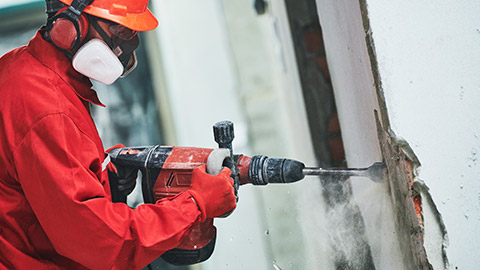
What we're covering:
- Safeguards for power tool use – tool safety, operating technique, cord safety, etc.
To ensure safety while using power tools, it is essential to follow safety guidelines, wear appropriate PPE, and undergo proper training on tool usage and maintenance. Regular inspections and a clean, organised workspace can also help minimise hazards and potential risks. Standards and best practices for using power tools are discussed below:
Tool Safety
The basic rules for using electrical tools safely include:
- Use the right tool for the job.
- Inspect each tool for damage before use. Never use a damaged tool - take damaged tools out of service immediately.
- Keep all tools in good condition with regular maintenance.
- Operate tools according to the manufacturer’s instructions.
- Wear the proper PPE.
- Do not remove or alter safety guards on an electrical tool.
- Disconnect power tools from the power source when not in use to prevent accidental activation.
- Keep power tools and cords away from water, liquids, and wet surfaces to avoid the risk of electrical shock.
- For power tools that require grounding, make sure they are connected to properly grounded outlets to prevent electrical shock.
Opt for power tools with double insulation – these tools offer an additional layer of safeguard against electric shock, particularly beneficial in cases of external insulation damage. To check if a tool is double insulated, look for the words "Double Insulated" or a double square symbol, which means it's designed with this added safety feature.
NEVER DO THIS!!!
Operating Technique
Be sure to keep good footing and maintain good balance when operating power tools. Avoid accidental starting. Do not hold fingers on the switch button while carrying a plugged-in tool. Always keep your hands firmly on the handles of the tools.
Wear proper PPE for the task and avoid loose clothing, jewelry, etc., that can become caught in moving parts.
Cord Safety
When it comes to using power tools, electrical cord safety is a vital consideration and it's important to adhere to proper safety practices:
Keep cords away from heat sources, liquids, and sharp edges to prevent potential hazards.
Check cords and plugs regularly for any signs of damage, fraying, or exposed wires. Do not use tools with damaged cords or plugs. Secure cords in place using cable ties or clips to prevent tripping hazards. When using extension cords, ensure they match the power requirements of the tool in use.
De-Energise Equipment
Before performing maintenance or changing accessories on power tools, you must disconnect them from the power source to prevent accidental activation.
Avoid Overloading Circuits
Do not overload electrical circuits by connecting too many tools to a single outlet. Overloading can lead to overheating, fires, or tripped circuit breakers. Also ensure the power tool matches the electrical system's voltage and frequency to avoid overload.
Use RCDs
Residual Current Devices cut off power if any current leakage is detected, ensuring a safer working environment. They provide an extra layer of protection against electric shock. Use portable RCDs for power tools if necessary. Ensure they are properly installed and regularly checked for functionality.
Work Area Organization
Adequate lighting, ergonomic workstations, and good housekeeping help to ensure power tool safety. Ensure the work area is well-lit and organised. Clear away clutter and debris that could cause tripping hazards or obstruct the use of power tools. Keep everyone not involved in the work at a safe distance from the work area.
Lockout/Tagout
When performing maintenance or repairs on electrical equipment, use lockout/tagout procedures to isolate the equipment from the power source to prevent accidental start-up.
Training and Education
Ensure that all individuals using power tools receive proper training on electrical safety, including recognizing hazards and using appropriate PPE. Workers should be trained in the proper use of all electrical tools they may be required to use.
Test and Tag
Electrical equipment on building sites must be tested and tagged every 3 months. See standard AS/NZS 3012:2019 Electrical installations - Construction and demolition sites. The tag should give the date of the inspection and the next date an inspection is due.
Circuit Breakers
Install circuit breakers to prevent circuit overloads and protect the power tool from electrical surges.
Emergency Stop System
The power switch installed in most power tools is not easy to reach in emergency situations. Employers should, therefore, implement an emergency stop system.
Risk assessments
Providing routine risk assessments of the workplace can help employers reduce power tool-related accidents and injuries.
Environmental Factors
- Do not use power tools in damp or wet locations unless they are approved for that purpose.
- Use equipment suitable for the working environment, e.g., cordless tools for damp conditions.
- All electrical connections for electrical tools must be suitable for the type of tool and the working conditions (wet, dusty, flammable vapors).
- If a portable electrical appliance is used in damp situations, it must have the following safeguards:
- An isolating transformer with a voltage between conductors not exceeding 230 volts.
- Double insulation to the appliance.
- A source to earth connection so that the earth voltage does not exceed 55 volts.
- An RCD to monitor the electric current flowing through the circuit. (If you touch a live wire or faulty equipment and electricity flows through you to the ground, the RCD senses the reduction in current and shuts off the electricity. This reduces the risk of a serious or fatal injury.)
Activity
You're tasked with using an angle grinder for electrical installation work. Complete the activity by adding your own descriptions of the safety measures that you should implement to ensure your safety and proper use of the angle grinder. When you have finished making your notes, you can export and save them as a document on your device.
Activity
Watch this series of CITBSA videos on tool safety to confirm you are now well-informed about working safely with both hand and power tools. Make notes for yourself on the most important tips you hear in the videos.
Hand Cutting Tools Safety
Power Saws Tools Safety
Drills Tool Safety
Grinders Tool Safety
Watch
Hand Cutting Tools Safety
This video is about the safe use of hand tools that are used for cutting different materials.
Duration: 5.29
Questions
Pre-Watch Question: Before you watch, what are three pieces of advice that you would give to a classmate to help keep them safe while using hand tools that cut? Then when you listen, is your advice covered by the video content?
Post Watch Task: Write down three pieces of advice from the video that is different to the advice you would give your classmate from the pre-watch question.
Watch
Power Saws Tools Safety
This video is from the same series as the hand tools ones that you have just watched, but this one covered powered saw safety.
Duration: 5.28
Questions
Pre-Watch Question: What are three hazards of using power saws?
Post Watch Task: Do you need different PPE when using power saws compared to hand cutting tools? Why?
Watch
Drills Tool Safety
This is also from the same series of safety videos and covers the safe use of power drills.
Duration: 2.19
Questions
Pre-Watch Question: Do you think that there will be a difference in the risks and hazards of using power drills compared to power saws?
Post Watch Task: Write down the steps for checking and using a power drill safely.
Watch
Grinders Tool Safety
This is from the same series of video on tool safety as the three above. The topic for this one is safe use of power tools that grind materials.
Duration: 5.49
Questions
Pre-Watch Question: List the hazards and risks that you think will be covered in this video.
Post Watch Task: Compare what you wrote with what you saw in the video. Did you miss anything?
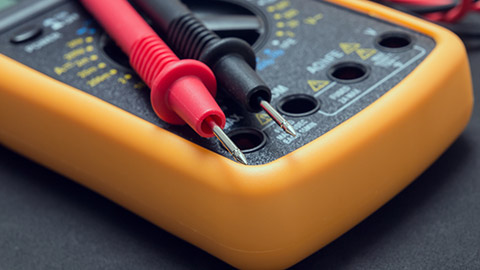
What we're covering:
- Meters and testers - multifunction, voltage tester, IR, multi-meter, clamp-on ammeter, phase rotation, circuit finders, line locators.
- AS/NZS 3017:2022 AS/NZS 3760:2022
The scope of electrical work you engage in, as well as the testing requirements, will determine the specific type of test equipment you will need in your tool kit.
Remember that after checking an electrical installation visually, tests should be carried out in accordance with AS/NZS 3000:2018, Clause 8.3.3. These tests make sure the installation meets the standard requirements and is safe for its intended use.
You must adhere to the Electricity (Safety) Regulations, ESR 63 and ESR 90, which mandate testing for all prescribed electrical work on installations and appliances and in order to perform these tests effectively, you must possess suitable and compliant test equipment.
AS/NZS 3017:2022 is a guide for inspecting and testing low voltage electrical setups. It ensures they comply with safety rules to prevent fires and protect people and animals from electric shocks. This guide applies to installations connected to an MEN system. Use AS/NZS 3017:2022 to meet the Periodic Verification needs of both the Electricity (Safety) Regulations 2010 and AS/NZS 3019:2007. It contains helpful checklists for visual inspection and testing, which electricians should keep handy. By using these checklists along with AS/NZS 3000:2018, you can ensure electrical setups are safe and meet the standards.
Selecting the right test equipment:
- Assess Your Testing Needs: Consider the specific tests you will need to conduct. Understanding your requirements will help you make informed decisions when choosing the appropriate equipment. (See the table below.)
- Conduct Research: Before making any purchases, conduct thorough research. Seek advice from experienced electrical practitioners and explore various suppliers of testing equipment. Evaluate whether a particular meter is fit for your intended purpose, ensuring it offers accuracy, appropriate overvoltage category rating (cat rating), suitable resolution, test values, and the required ranges.
- Comprehend Specifications: Review the specifications of potential test equipment. If you don't understand some of the technical jargon, seek guidance from someone knowledgeable in the field. Understanding these specifications is crucial to selecting the right tools.
- Choose Reputable Brands: Select reputable and reliable brands known for producing robust, good-quality equipment. Additionally, look for products that come with after-sales warranties, providing you with added assurance.
The following table, created by the Electrical Workers Registration Board summarises the types of test instrument required for various measurements:
Testing Instrument measuring | ||
---|---|---|
Voltage AC and DC | Dedicated voltage tester. | Should be capable of reading all working voltages, both AC&DC. |
Resistance | 500V DC Insulation resistance (IR) tester or incorporated in multifunction tester. | For testing a 400V 3 phase or 230V single phase installation a 500V DC test voltage is required as a minimum. |
Resistance | Multi-meter or incorporated in multifunction tester. | Multi-meter should be rated Cat III. |
Current | Clamp-on Ammeter. | Cat III clamp-on ammeter capable of reading all load requirements. |
Leakage Current | Leakage current clamp-on Ammeter. | Cat III high resolution clamp-on ammeter capable of milliamps. |
Fault Loop-Impedance | Incorporated in multifunction tester. | Cat III or IV. |
RCD Testing | Incorporated in multifunction tester. | Capable of 30mA and 10mA RCD tests. |
Phase Rotation | Phase rotation tester. | Contactless meter offers more safety. |
MULTIFUNCTION TESTER
Multifunction testers are widely available from major electrical test equipment manufacturers. You can easily find information about different brands and models by searching online or asking electrical wholesalers for guidance.
The main advantage of multifunction testers is that they combine multiple testing functions in one device. This makes it efficient for electrical workers to perform all the necessary tests required to meet AS/NZ Standards and regulations. It simplifies the testing process and is useful for various electrical tasks.
While multifunction testers can do many tests, it's also helpful to consider having separate specialised tools for specific tasks. This can improve precision and efficiency, especially for complex projects. Having separate instruments can act as a backup in case one fails, ensuring work continues without interruptions. Additionally, using separate meters for different jobs can boost productivity, enabling multiple tasks to be done simultaneously. This is particularly useful for bigger projects or when multiple teams are working together.
Some of the key functions performed by multifunction testers include:
- Insulation Resistance Testing: This test measures the resistance between conductive parts and the earth, ensuring the effectiveness of insulation in electrical circuits and identifying potential leakage paths or insulation breakdowns.
- Earth Loop Impedance Testing: Earth loop impedance testing evaluates the impedance or resistance of the earth connection in the event of a fault, ensuring that fault currents can be safely discharged, minimising the risk of electric shock.
- RCD (Residual Current Device) Testing: RCDs are critical safety devices that protect against electric shocks by rapidly disconnecting the power supply during a fault. Multifunction testers can verify the proper functioning and safety limits of these devices.
- Polarity Testing: Polarity testing checks the correct connections of live, neutral, and earth conductors in an electrical system. Proper polarity ensures that electrical appliances and equipment function as intended, reducing the risk of electrical faults.
- Continuity and Resistance Measurement: Multifunction testers can measure continuity and resistance in electrical circuits, helping to detect loose connections, faulty wiring, or damaged components.
- Voltage and Current Measurement: These testers can also measure voltage and current in both AC and DC circuits, providing valuable information about the electrical system's performance.
- Phase Sequence Testing: In three-phase electrical systems, a multifunction tester can determine the correct sequence of phases, ensuring that motors and machinery run in the intended direction.
- Data Logging and Reporting: Many multifunction testers come equipped with data logging capabilities, allowing electricians to store test results for analysis and documentation. Detailed reports can be generated for compliance and regulatory purposes.
- Frequency and Capacitance Measurement: Some advanced multifunction testers offer additional functions, such as measuring frequency and capacitance, providing more comprehensive insights into electrical systems.
DEDICATED VOLTAGE TESTER
A voltage tester is a handheld device used to quickly check if a circuit or appliance is energised, before working on it. The simplest and safest type of voltage tester is the non-contact voltage tester, powered by batteries, which can detect electricity by being close to an outlet slot or wire.
It is essential to use a voltage tester to detect AC voltages on sockets, switches, outlets, and circuit breakers before commencing an electrical project.
The voltage tester's indicator, often a light-emitting diode (LED), illuminates if voltage is present, indicating the need to shut down the current before starting work. This is a vital safety measure required by health and safety legislation.
INSULATION RESISTANCE (IR) TESTER
An Insulation Resistance (IR) Tester is a specialised test instrument used to evaluate the integrity of insulation in electrical systems. The primary purpose of this tester is to detect insulation leakage between live conductors and between live conductors and earth. It helps electricians and electrical professionals identify potential faults, weaknesses, or breakdowns in the insulation of electrical circuits and appliances. It works by applying a test voltage to the circuit being examined and measuring the resistance of the insulation.
Regularly conducting insulation resistance tests is essential for maintaining the reliability and safety of electrical installations. Electricians often use the IR tester during maintenance, troubleshooting, and safety inspections to ensure that insulation is performing as expected. When using the IR tester, proper safety precautions must be followed, including de-energizing the circuit before performing the test.
According to AS/NZS 3000:2018 8.3.6.1, the IR tester must maintain the terminal voltage within +20% and -10% of the nominal open circuit voltage while measuring a resistance of 1 MΩ on the 500V range or 10 MΩ on the 1000V range.
MULTI-METER
A multimeter is a versatile digital tool combining multiple functions into a single device. It can read a wide range of electrical parameters, including:
- Voltage: Multimeters can measure both AC (alternating current) and DC (direct current) voltage. They are used to determine the potential difference between two points in an electrical circuit.
- Current: Multimeters can measure both AC and DC currents flowing in a conductor. They allow electricians to determine the amount of current passing through a circuit.
- Resistance: Multimeters can measure the resistance of an electrical component or circuit. Resistance refers to the opposition of current flow in a conductor.
- Continuity Testing: Multimeters can check for continuity, which determines if a circuit is complete and capable of conducting electricity. It is often used to identify open circuits or faulty connections.
- Diode Testing: Some multimeters have a diode testing function, which helps check the health of diodes in electronic circuits.
- Capacitance: Advanced multimeters can measure capacitance, which determines the ability of a component to store an electrical charge.
- Frequency: Certain multimeters can measure the frequency of an AC signal, which is the number of cycles per second.
- Temperature: Some multimeters come with temperature measurement capabilities, often using a thermocouple probe.
- Duty Cycle: Duty cycle measurement allows you to assess the percentage of time a digital signal is high (on) compared to the total period.
- Non-Contact Voltage Detection: Some multimeters have a non-contact voltage detection feature, which allows them to detect the presence of AC voltage without making direct contact.
CLAMP-ON AMMETER
Clamp-on ammeters are non-invasive electrical testing instruments used to measure AC and DC currents without disconnecting wires. They are similar to a standard tester or multimeter with the addition of a clamp/jaw that reads amperage on large diameter conductors. They offer a wide range of current measurement capabilities, and many models come with additional functions like voltage, resistance, frequency, and capacitance measurements. They are widely used in various industries for electrical maintenance, troubleshooting, and inspections. Proper safety precautions and regular calibration are essential for accurate and reliable readings.
PHASE ROTATION METER
Phase rotation meters, also known as phase sequence testers, are specialised electrical testing instruments used to identify the correct sequence of phases in a three-phase system. This is essential for ensuring the proper operation of motors, machinery, and other three-phase equipment.
Phase rotation meters often use non-contact testing methods, making them safe and easy to use. They can determine phase sequence without the need for physical contact with live conductors.
Many phase rotation meters feature LED indicators that display the correct phase sequence. These indicators may use arrows or numbers to show the proper sequence of phases. Some phase rotation meters also have audio indicators, such as buzzers or beeps, that provide an additional way to detect the phase sequence.
Phase rotation meters are suitable for both low-voltage and high-voltage applications, making them versatile tools for various electrical systems.
In addition to identifying phase sequence, phase rotation meters can also be used to test the rotation direction of three-phase motors, ensuring they are connected correctly.
Most phase rotation meters are portable and handheld, allowing electricians and technicians to easily carry them to different job sites.
CIRCUIT FINDERS
Circuit finders, also known as circuit tracers or circuit breakers finders, are used to locate the path of live electrical circuits in walls, ceilings, or floors. They are particularly useful for finding circuit breakers, tracing wiring paths, and locating electrical faults in complex wiring systems.
Circuit finders work based on the principle of electromagnetic field detection. When an electrical current flows through a conductor, it generates a magnetic field around it. The circuit finder's transmitter unit is connected to the electrical circuit or breaker panel. It injects a signal into the circuit, which creates a magnetic field along the path of the live wires. The handheld receiver unit is then used to detect the magnetic field and trace the path of the live wires, allowing electricians to identify the course of hidden electrical lines.
LINE LOCATORS
Line locators, also called line tracers or underground cable locators, are used to locate underground or buried electrical cables, pipes, or other conductive materials before excavation or construction work, preventing accidental damage to buried utilities. They work based on the principle of electromagnetic induction. When an alternating current is applied to an electrical cable, it generates an electromagnetic field around the cable.
The line locator's transmitter unit applies an alternating current to the cable, creating an electromagnetic field that radiates outward. The handheld receiver unit is then used to detect the electromagnetic field and pinpoint the location of the underground cable, allowing electricians to trace its path without digging.
A Final Word about Test Equipment Selection…
When choosing an electrical test instrument, it is essential to prioritize safety and ensure the meter is suitable for the intended use. Here are some key steps to follow:
- Understand Measurement Categories: Begin by identifying the measurement categories (Cat II, Cat III, Cat IV) suitable for your specific tasks. This ensures that the test instrument is appropriate for the electrical environment it will be used in.
- Verify Electrical Safety Standards: Look for the correct electrical safety standard applicable to the test instrument you need. Ensure it complies with the relevant safety regulations to guarantee safe operation.
- Seek Independent Type Testing: Check if the test instrument has undergone independent type testing to the safety standard mentioned. This provides assurance that the meter meets safety requirements and has been rigorously tested.
- Check Warning Labels and Markings: Inspect the test instrument for warning labels or markings that indicate its safe use, potential hazards, and operating instructions. Adhere to these instructions to prevent accidents or damage.
- Review Specifications: Examine the meter's specifications to assess its performance capabilities objectively. Pay close attention to accuracy, resolution, range, and precision, considering all these factors together to make an informed decision.
- Ensure your test instruments undergo annual testing and recalibration by an approved supplier to maintain their accuracy at an acceptable level. It's crucial that your test instrument carries a calibration certificate; otherwise, recorded results may become invalid.
- To keep your meter operational and safe, periodically verify its accuracy. For common (non-specialist) meters used in regular installation work, routine accuracy checks of calibration are straightforward and quick. It's highly recommended to perform these checks regularly and document the results. However, if you find that the meter is out of calibration, you should send it to an accredited laboratory for correction. These routine checks are not a substitute for accredited calibration.
AS/NZS 3760:2022 – Ensuring electrical safety through in-service inspection and training
Introduction
AS/NZS 3760:2022 plays a vital role in promoting electrical safety and compliance with regulations in Australia and New Zealand. This standard serves as the foundation for testing and tagging electrical equipment, with a strong emphasis on ensuring user safety.
Scope and Applicability
AS/NZS 3760:2022 is applicable throughout the lifecycle of electrical equipment. It addresses situations when equipment is put into service for the first time, in use, available for second-hand sale or hire, or has undergone servicing or repair. This latest version focuses on inspection and testing guidelines for Class I and Class II appliances, functional earthing, insulation, leakage current, RCD tripping times, cord sets, and earth continuity resistance.
Safety Focus
The primary objective of AS/NZS 3760:2022 is to guarantee the safety of electrical equipment used in diverse settings, including workplaces, homes, and public spaces. The standard outlines a systematic approach to inspecting and testing electrical equipment, aiming to identify defects, damage, or wear that could lead to unsafe conditions. By concentrating on safety concerns, AS/NZS 3760 ensures that equipment remains electrically sound and properly connected, minimising the risks of electric shock and fire hazards.
Inspection and Testing Procedures
AS/NZS 3760:2022 outlines comprehensive testing procedures, including visual inspections, insulation resistance tests, earth continuity tests, and polarity tests. These measures serve to assess the equipment's condition and its ability to prevent hazards effectively. The standard's emphasis on visual inspections, which can detect over 90% of defects, accounts for environmental hazards and the equipment's wear during testing.
Frequency of Inspections
The recommended inspection and testing frequencies within AS/NZS 3760:2022 are contingent upon equipment type, intended use, and environmental conditions. Regular inspections and testing are crucial in identifying and rectifying potential issues before they escalate into more serious safety risks.
Record Keeping and Compliance
hAS/NZS 3760:2022 necessitates the maintenance of records detailing testing outcomes, including the tester's name, testing date, results, and the next scheduled testing date. This record-keeping system ensures accountability and traceability, contributing to overall compliance with safety regulations.
Role in Workplace Safety
AS/NZS 3760:2022 assumes a pivotal role in workplace safety by overseeing the Test and Tag industry regarding portable appliance electrical safety. It sets recommendations for testing various types of electrical equipment commonly found in workplaces, emphasizing test and tag frequencies, inspection and testing specifications, and record-keeping guidelines.
Activity
Let’s review the key points of AS/NZS 3760:2022. Complete the learning activity below.
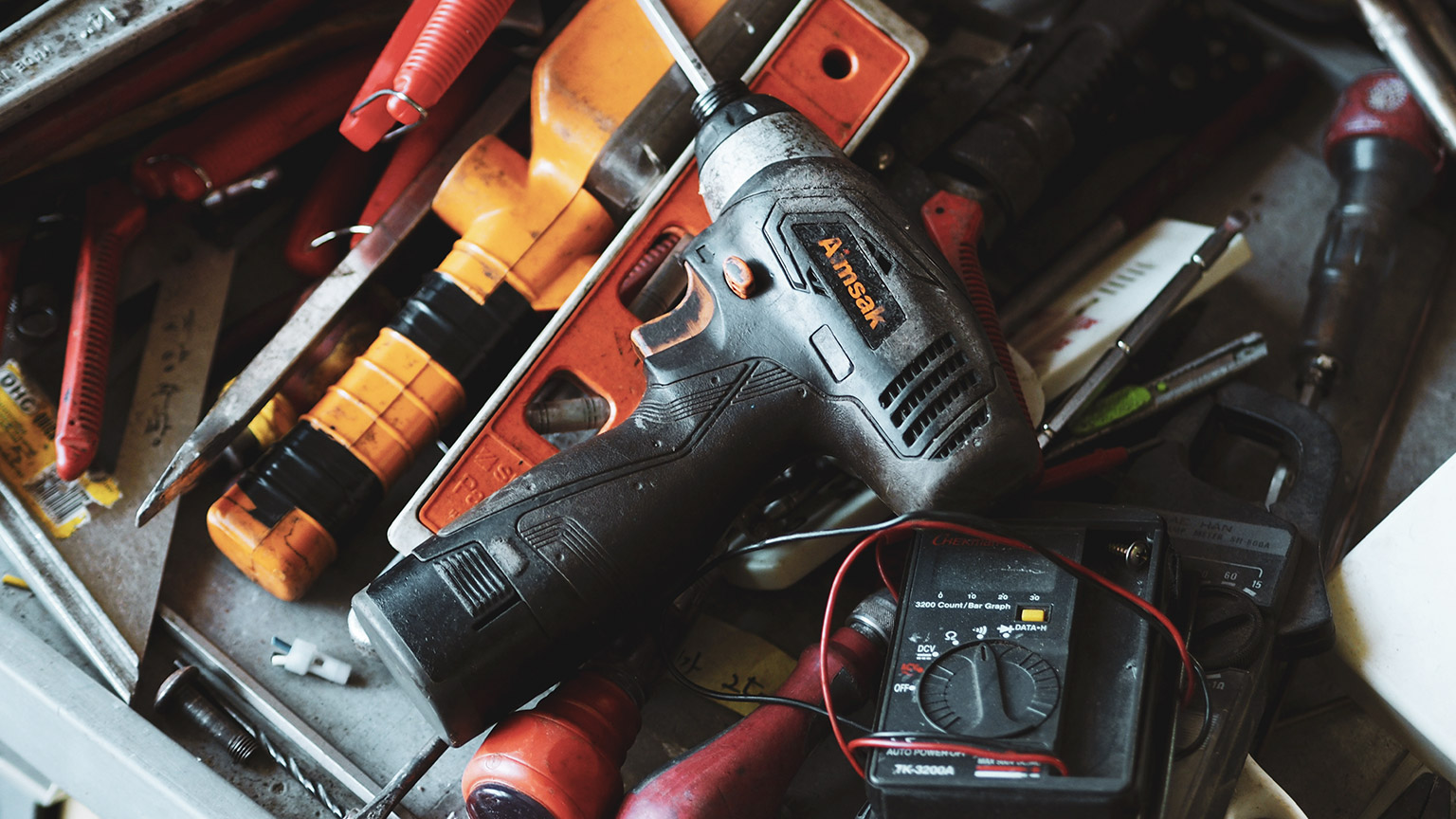